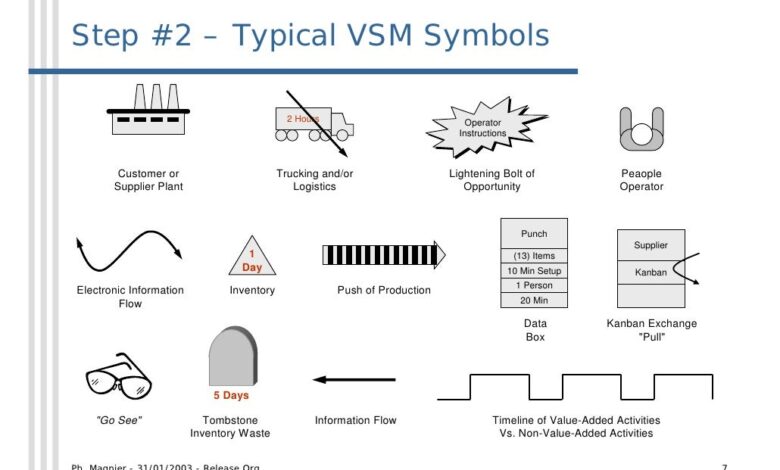
Who Is VSM For? Unlocking Value Stream Mapping
Who is VSM for? That’s the question we’ll be tackling today, and the answer might surprise you! Value Stream Mapping (VSM) isn’t just for manufacturing giants; it’s a powerful tool that can benefit a surprisingly wide range of businesses and individuals. Whether you’re a project manager struggling with bottlenecks, a healthcare professional aiming to streamline patient flow, or a software developer looking to optimize your development lifecycle, VSM offers a fresh perspective and practical strategies for improving efficiency and reducing waste.
This post delves into the specific applications, benefits, and challenges of implementing VSM, so you can decide if it’s the right fit for you.
We’ll explore how VSM is applied across diverse sectors, from manufacturing and healthcare to software development and beyond. We’ll also examine the core principles of VSM, providing a clear understanding of its methodology and the steps involved in creating and implementing a VSM map. Finally, we’ll address common challenges and offer practical solutions to help you navigate the implementation process successfully.
Get ready to discover how VSM can transform your workflow and unlock significant improvements in your organization!
VSM Target Audience
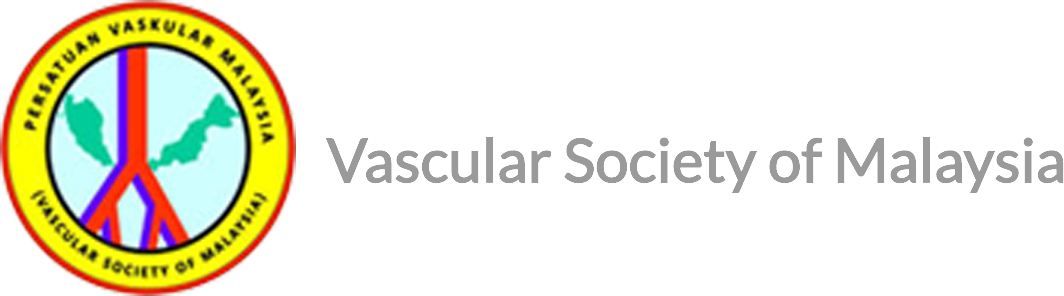
Value Stream Mapping (VSM) isn’t a one-size-fits-all solution. Its effectiveness hinges on understanding and addressing the specific needs of the user. Identifying the ideal VSM user profile allows for targeted implementation and maximizes the return on investment.
A typical VSM user often works within operational excellence, process improvement, or lean management roles. They are typically found in manufacturing, healthcare, or service industries, but the methodology’s adaptability makes it valuable across a wide range of sectors. Company size isn’t a limiting factor; VSM can benefit small businesses striving for efficiency as much as large corporations seeking to streamline complex processes.
The key characteristic is a desire for continuous improvement and a willingness to collaboratively analyze and optimize workflows.
VSM Challenges Addressed by User Groups
The challenges VSM addresses vary depending on the user’s specific context. For example, a manufacturing plant might use VSM to identify and eliminate bottlenecks in their production line, leading to increased throughput and reduced lead times. In healthcare, VSM can be used to optimize patient flow, reducing wait times and improving overall patient experience. In a service industry context, a call center might leverage VSM to streamline its call handling process, improving customer satisfaction and agent efficiency.
The common thread is the identification and elimination of waste within a process.
Examples of Successful VSM Implementations
Numerous organizations have successfully implemented VSM, achieving significant improvements. Consider a hypothetical case study of a mid-sized manufacturing company that used VSM to identify and eliminate a bottleneck in their assembly line. By mapping the entire process, they pinpointed a specific step that was causing significant delays. Through process redesign and improvements in material handling, they were able to reduce lead times by 20% and increase output by 15%.
Similarly, a large hospital system used VSM to analyze its emergency room workflow, resulting in a significant reduction in patient wait times and improved patient satisfaction scores. These are just two examples showcasing the versatility and impact of VSM across various sectors.
VSM Benefits Across User Profiles
The table below summarizes the key benefits of VSM for different user profiles, highlighting the tailored advantages based on their specific roles and organizational contexts.
User Profile | Key Benefit 1 | Key Benefit 2 | Key Benefit 3 |
---|---|---|---|
Manufacturing Plant Manager | Increased Production Efficiency | Reduced Lead Times | Improved Inventory Management |
Healthcare Process Improvement Specialist | Reduced Patient Wait Times | Improved Patient Flow | Enhanced Patient Satisfaction |
Service Industry Operations Manager | Improved Customer Service | Increased Employee Productivity | Reduced Operational Costs |
Project Manager | Improved Project Planning & Execution | Reduced Project Cycle Times | Enhanced Risk Management |
VSM Applications and Use Cases
Value Stream Mapping (VSM) isn’t just a theoretical framework; it’s a powerful tool with widespread applicability across diverse industries. Its core principle – identifying and eliminating waste – translates effectively into tangible improvements in efficiency and productivity, regardless of the specific business context. This section explores how VSM is used in various sectors and showcases real-world examples of its successful implementation.VSM’s adaptability stems from its focus on the flow of value from a customer’s perspective.
By visualizing the entire process, from initial request to final delivery, VSM allows organizations to pinpoint bottlenecks, redundancies, and areas ripe for optimization. This approach transcends industry-specific jargon, making it a valuable tool for any organization committed to process improvement.
VSM in Manufacturing
Manufacturing environments are ideal candidates for VSM implementation. The highly structured nature of production processes allows for clear identification of value-added and non-value-added activities. For instance, a car manufacturer might use VSM to map the assembly line, identifying delays caused by parts shortages or inefficient workstation layouts. By visualizing the entire process, they can pinpoint areas where inventory is unnecessarily high, reducing storage costs and freeing up capital.
Toyota, a pioneer of Lean manufacturing, heavily utilizes VSM to continuously improve its production processes, resulting in significantly reduced lead times and increased efficiency. A successful VSM implementation in this context might involve reducing the number of steps in the assembly process, optimizing inventory levels, and improving communication between different departments.
VSM in Healthcare
In healthcare, VSM can be used to streamline patient care processes, reducing wait times and improving patient outcomes. Consider a hospital using VSM to map the process of admitting a patient. The map might reveal bottlenecks in the registration process, delays in obtaining test results, or inefficiencies in communication between different medical staff. By identifying these bottlenecks, the hospital can implement improvements such as electronic health records, optimized scheduling systems, and improved communication protocols.
The Mayo Clinic, for example, has successfully used VSM to improve its operational efficiency and patient flow, leading to significant reductions in wait times and improved patient satisfaction. This might involve reducing handoffs between departments, implementing better communication tools, and improving the overall patient experience.
VSM in Software Development
Even in the seemingly less tangible world of software development, VSM proves valuable. By mapping the entire software development lifecycle, from initial requirements gathering to final deployment and maintenance, development teams can identify bottlenecks and inefficiencies. For example, a software company might use VSM to map the process of developing a new feature, identifying delays caused by inefficient coding practices, lengthy testing cycles, or communication breakdowns between developers and testers.
This visualization helps identify areas for improvement, such as implementing agile methodologies, improving code quality, and enhancing communication. Companies like Spotify have adopted VSM principles to streamline their software development processes, leading to faster release cycles and improved product quality. This often includes focusing on continuous integration and continuous delivery (CI/CD) to reduce deployment times and improve the overall software development process.
VSM Implementation Flowchart: Manufacturing Example
The following describes a flowchart illustrating the step-by-step implementation of VSM in a manufacturing setting. Imagine a simplified example focusing on a single product line. Step 1: Define the Scope: Clearly define the specific product or process to be mapped. This could be the entire assembly line for a specific product or a sub-process within the larger manufacturing operation. Step 2: Gather Data: Collect data on the current state of the process, including cycle times, inventory levels, and defect rates.
This might involve observing the process, interviewing workers, and reviewing production records. Step 3: Create the Current State Map: Draw a visual representation of the current state, including all steps, material flows, and information flows. This map will highlight areas of waste and inefficiency. Step 4: Identify Waste: Analyze the current state map to identify different types of waste, such as excess inventory, waiting time, transportation, overproduction, etc.
Use Lean principles to categorize these wastes. Step 5: Develop Future State Map: Design a future state map showing how the process can be improved by eliminating or reducing identified waste. This might involve streamlining processes, reducing inventory, or improving communication. Step 6: Implement Improvements: Implement the changes Artikeld in the future state map. This may involve changes to equipment, processes, or worker training.
Step 7: Monitor and Measure: Continuously monitor the process to ensure that the implemented changes are effective and to identify any new areas for improvement. Track key metrics to demonstrate the impact of the VSM implementation.
VSM Benefits and Value Proposition

Value Stream Mapping (VSM) offers a powerful approach to process improvement, going beyond simple efficiency gains to deliver significant strategic advantages. By visualizing the entire flow of materials and information, VSM reveals hidden inefficiencies and bottlenecks that traditional management methods often miss. This holistic perspective allows for targeted interventions that optimize the entire system, not just individual components.VSM’s strength lies in its ability to provide a clear, concise, and actionable roadmap for improvement.
Unlike methods that focus on isolated problem-solving, VSM facilitates a collaborative, cross-functional approach, engaging all stakeholders in the process improvement journey. This shared understanding fosters ownership and commitment, leading to more sustainable and effective change.
Comparison of VSM with Other Methodologies
VSM shares similarities with Lean and Six Sigma, but possesses unique characteristics. Lean focuses on eliminating waste and maximizing value from the customer’s perspective, while Six Sigma emphasizes reducing variation and improving process capability. VSM complements both by providing a visual tool to identify and analyze the sources of waste and variation within the entire value stream. While Lean might identify a problem area, VSM provides the detailed map to understand its root causes and implement effective solutions.
Similarly, Six Sigma might focus on statistical process control, but VSM provides the context to understand where and why those controls are necessary. VSM integrates the principles of both methodologies, offering a comprehensive approach to process optimization.
Measurable Improvements from VSM Implementation
Organizations implementing VSM can expect significant measurable improvements across various key performance indicators (KPIs). These improvements are not merely hypothetical; numerous case studies demonstrate tangible results. For example, a manufacturing company might reduce lead times by 30% by identifying and eliminating bottlenecks in their production process as revealed by the VSM. Similarly, a service organization could improve customer satisfaction scores by 15% by streamlining their service delivery process and reducing wait times.
The improvements are not limited to operational efficiency; they also extend to improved quality, reduced costs, and increased profitability.
Quantifiable Benefits of VSM
The benefits of VSM are readily quantifiable and demonstrably impactful on the bottom line.
- Reduced Lead Times: By identifying and eliminating bottlenecks, VSM can significantly shorten the time it takes to deliver products or services. For example, a company might reduce its order fulfillment time from 10 days to 5 days, improving customer satisfaction and freeing up resources.
- Improved Quality: VSM helps identify and eliminate sources of defects and errors, leading to improved product or service quality. A reduction in defects can translate directly to lower rework costs and improved customer loyalty.
- Increased Profitability: The combined effect of reduced lead times, improved quality, and reduced waste translates directly into increased profitability. Savings from reduced inventory, lower operating costs, and improved efficiency contribute to a healthier bottom line.
- Reduced Inventory: By optimizing the flow of materials, VSM minimizes the need for large inventories, reducing storage costs and the risk of obsolescence. This frees up capital for other investments.
- Improved Employee Morale: The collaborative nature of VSM and the visible progress made towards improvement often lead to increased employee engagement and satisfaction.
Understanding VSM Principles and Methodology
Value Stream Mapping (VSM) is a lean manufacturing technique used to visually represent the flow of materials and information required to bring a product or service to the customer. It’s a powerful tool for identifying waste and bottlenecks, leading to significant process improvements. Understanding the core principles and methodology is crucial for effective VSM implementation.VSM relies on a set of fundamental principles rooted in lean thinking.
These principles guide the creation and interpretation of the map, ensuring that the resulting analysis is accurate and actionable. The process focuses on understanding the current state, identifying areas for improvement, and then designing and implementing a future state map that reflects the desired improvements. This iterative approach allows for continuous refinement and optimization of the value stream.
Core Principles of VSM
The core principles guiding VSM are built around eliminating waste and maximizing value. These principles directly inform the methodology used to create and interpret VSM maps. Effective VSM implementation hinges on a deep understanding and application of these core concepts.
- Value Definition: Clearly defining what constitutes value from the customer’s perspective is paramount. This ensures that all efforts are focused on activities that directly contribute to customer satisfaction.
- Waste Identification: VSM highlights various types of waste (Muda) such as transportation, inventory, motion, waiting, overproduction, over-processing, and defects. Identifying these wastes is the first step towards eliminating them.
- Flow Optimization: The goal is to create a smooth, continuous flow of materials and information, minimizing interruptions and delays. This involves streamlining processes and eliminating bottlenecks.
- Process Visualization: VSM provides a visual representation of the entire value stream, making it easy to identify areas for improvement and track progress over time. This visual representation facilitates communication and collaboration among team members.
- Continuous Improvement (Kaizen): VSM is not a one-time exercise. It’s an iterative process that supports continuous improvement through regular reviews and updates of the map.
Steps Involved in Creating a VSM Map
Creating a VSM map is a systematic process involving several key steps. Each step builds upon the previous one, culminating in a comprehensive visual representation of the value stream. The process involves both data collection and collaborative analysis.
- Define the Scope: Clearly define the product or service and the boundaries of the value stream to be mapped. This includes specifying the starting and ending points of the process.
- Gather Data: Collect data on process times, inventory levels, lead times, and other relevant metrics. This data forms the basis for the VSM map.
- Create the Current State Map: Draw the current state map, using standard VSM symbols to represent different process steps, inventory, transportation, etc. This visual representation shows the current flow of materials and information.
- Analyze the Current State Map: Analyze the current state map to identify bottlenecks, waste, and areas for improvement. This involves calculating lead times, identifying process inefficiencies, and pinpointing areas where value is not being added.
- Develop the Future State Map: Based on the analysis of the current state, develop a future state map that reflects the desired improvements. This map should show how the process will look after implementing changes to eliminate waste and improve efficiency.
- Implement and Monitor: Implement the changes identified in the future state map and monitor the results. Regularly review and update the map to reflect ongoing improvements.
Creating a Basic VSM Map: A Step-by-Step Guide
Let’s illustrate a simplified example. Imagine a small bakery making bread. We’ll map the process from flour delivery to bread delivery to the customer.
- Scope Definition: The process starts with flour delivery and ends with bread delivery to the customer.
- Data Gathering: We collect data on flour delivery time, mixing time, proofing time, baking time, cooling time, packaging time, and delivery time to the customer.
- Current State Map: We would draw a map showing each step as a rectangle, inventory as a triangle, transportation as an arrow, and use standard VSM symbols (detailed below) to represent the flow.
- Analysis: We identify potential bottlenecks, for example, long baking time or insufficient cooling capacity.
- Future State Map: We propose solutions like investing in a faster oven or adding more cooling racks to reduce bottlenecks and improve the overall flow.
- Implementation & Monitoring: We implement the changes and track the impact on lead time and efficiency.
Common VSM Symbols and Notations
Understanding the symbols used in VSM is crucial for interpreting the map effectively. Consistent use of these symbols ensures clear communication and understanding across teams.
- Rectangle: Represents a process step. This could be mixing, baking, packaging, etc.
- Triangle: Represents inventory (raw materials, work-in-progress, finished goods).
- Arrow: Represents transportation or movement of materials.
- Data Box: Contains information such as processing time, inventory levels, lead time, and other relevant metrics.
- Circle: Represents a delay or waiting time.
- Diamond: Represents a decision point or branching in the process.
Overcoming Challenges in VSM Implementation: Who Is Vsm For
Implementing Value Stream Mapping (VSM) can be a transformative experience, streamlining processes and boosting efficiency. However, the journey isn’t always smooth. Organizations often encounter significant hurdles during VSM implementation, hindering its potential benefits. Understanding these challenges and proactively developing mitigation strategies is crucial for successful VSM adoption.
Resistance to Change
Resistance to change is a common obstacle in any organizational transformation, and VSM implementation is no exception. Employees accustomed to established processes may view VSM as a threat, fearing job losses, increased workload, or disruption to their routines. This resistance can manifest as passive non-compliance, active opposition, or simply a lack of engagement. Addressing this requires a multifaceted approach focusing on communication, training, and participation.
Open communication about the benefits of VSM, involving employees in the mapping process, and providing thorough training on the new methods can significantly reduce resistance. Demonstrating early wins and celebrating successes along the way helps build momentum and encourage buy-in.
Lack of Management Support
Successful VSM implementation requires strong leadership support and commitment from top management. Without this backing, initiatives can stall due to insufficient resources, conflicting priorities, or a lack of accountability. Management’s role is not just providing resources but actively championing the VSM initiative, fostering a culture of continuous improvement, and ensuring alignment with overall organizational goals. This commitment should be visible through active participation in workshops, providing necessary resources, and consistently reinforcing the importance of VSM across the organization.
Data Collection and Analysis Challenges
Accurate and comprehensive data is essential for effective VSM. Gathering this data can be challenging, requiring careful planning, consistent data collection methods, and potentially the development of new data collection systems. Inaccurate or incomplete data can lead to flawed maps and ineffective improvement initiatives. Strategies to overcome this include identifying key data points upfront, establishing clear data collection protocols, utilizing existing data sources whenever possible, and employing data analysis tools to ensure accuracy and consistency.
Scope Definition and Team Selection
Defining the scope of the VSM project and selecting the right team are crucial initial steps. A scope that is too broad can overwhelm the team, while a scope that is too narrow may not yield significant results. The team should include representatives from all relevant departments and possess the necessary skills and authority to make changes. Careful consideration of these factors ensures a manageable project with the potential for meaningful impact.
Employing a phased approach, starting with a smaller, well-defined scope, can be beneficial for building team expertise and demonstrating early successes.
Sustaining Improvements, Who is vsm for
Implementing VSM is just the first step; sustaining the improvements identified through the mapping process is equally important. This requires establishing a culture of continuous improvement, incorporating VSM into daily operations, and regularly reviewing and updating the maps. Without ongoing monitoring and adjustments, the benefits of VSM can gradually erode. Regular kaizen events, standardized work practices, and the use of visual management tools can help maintain improvements over time.
Table of VSM Implementation Challenges and Solutions
Challenge | Solution | Impact | Mitigation Strategy |
---|---|---|---|
Resistance to Change | Effective communication, training, and employee involvement | Increased buy-in, smoother implementation | Develop a comprehensive change management plan |
Lack of Management Support | Secure executive sponsorship and allocate sufficient resources | Faster implementation, higher success rate | Present a strong business case for VSM |
Data Collection Difficulties | Establish clear data collection protocols and utilize appropriate tools | Accurate mapping and effective improvement initiatives | Pilot test data collection methods before full-scale implementation |
Inadequate Scope Definition | Start with a small, well-defined scope and gradually expand | Manageable project, faster results | Use a phased approach and iterative improvements |
Difficulty Sustaining Improvements | Establish a culture of continuous improvement and regular reviews | Long-term benefits and sustained efficiency gains | Implement visual management systems and regular kaizen events |
Closure
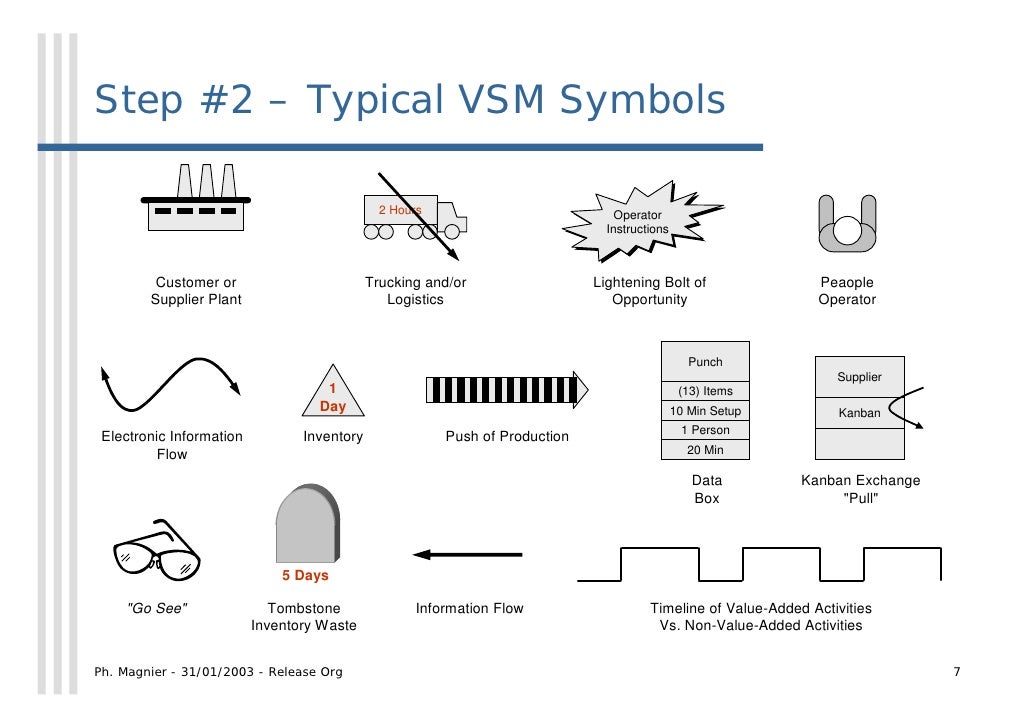
So, who
-is* VSM for? The short answer is: anyone looking to optimize their processes and eliminate waste. Whether you’re a small business owner or a leader in a large corporation, VSM provides a framework for understanding and improving the flow of value within your organization. By understanding your value stream, identifying bottlenecks, and implementing targeted improvements, you can unlock significant gains in efficiency, quality, and profitability.
While implementation might present some challenges, the potential rewards make VSM a worthwhile investment for a wide range of industries and organizations. Start exploring your own value stream today – you might be surprised at what you discover!
FAQ Resource
What is the difference between VSM and Lean?
VSM is a
-tool* used within the broader Lean methodology. Lean focuses on eliminating waste in all forms, while VSM provides a visual representation of the value stream to pinpoint areas for improvement.
Is VSM suitable for small businesses?
Absolutely! VSM’s benefits scale, making it applicable to businesses of all sizes. Even small teams can benefit from visualizing their processes and identifying bottlenecks.
How long does it take to implement VSM?
Implementation time varies depending on the complexity of the process and the size of the organization. Simple processes can be mapped relatively quickly, while larger, more complex processes may require more time.
What software can I use for VSM?
Many software options exist, from simple diagramming tools like Lucidchart or draw.io to specialized VSM software. The best choice depends on your needs and budget.