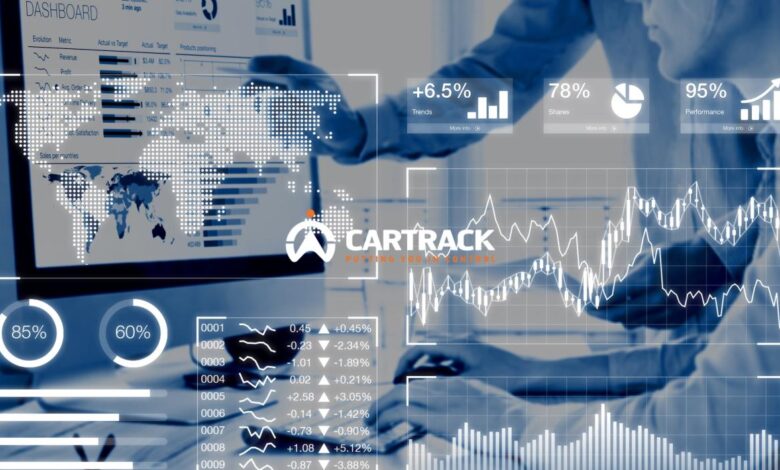
Aftermarket Cloud FSM Off-Highway Revolutionizing Maintenance
Aftermarket cloud fsm offhighway – Aftermarket Cloud FSM Off-Highway – it’s a mouthful, I know! But this technology is quietly revolutionizing how we maintain heavy machinery. Imagine a world where tracking equipment performance, scheduling maintenance, and managing technicians is all streamlined through a single, cloud-based system. That’s the power of aftermarket cloud FSM for off-highway vehicles, and it’s changing the game for businesses across industries.
This post dives deep into the current state of this market, exploring the key players, the technological advancements driving its growth, and the significant benefits it offers. We’ll also tackle the challenges, examine future trends, and look at real-world examples of successful implementations. Get ready to discover how cloud-based fleet service management is transforming the off-highway equipment landscape.
Market Overview of Aftermarket Cloud FSM for Off-Highway Equipment: Aftermarket Cloud Fsm Offhighway

The aftermarket cloud Fleet Service Management (FSM) market for off-highway equipment is experiencing significant growth, driven by increasing demand for improved operational efficiency and reduced downtime in demanding industries like construction, mining, and agriculture. This trend is fueled by the rising adoption of connected vehicles and the availability of affordable, robust cloud-based solutions. While precise market sizing is difficult due to the fragmented nature of the industry, analysts predict substantial expansion in the coming years, with double-digit growth rates not uncommon.
Key Players and Market Share
Determining exact market share for each player in this niche is challenging due to the lack of publicly available, comprehensive data. However, several prominent companies are making significant inroads. These include established enterprise resource planning (ERP) vendors expanding their offerings into FSM, specialized off-highway equipment manufacturers integrating FSM into their service offerings, and independent software vendors (ISVs) focusing solely on FSM solutions for this sector.
While precise figures are unavailable, the competitive landscape is characterized by a mix of large, established players and agile, specialized startups vying for market dominance. The market is likely consolidating, with larger players acquiring smaller ones to expand their capabilities and market reach.
Types of Off-Highway Equipment Utilizing Cloud-Based FSM
A wide range of off-highway equipment is benefiting from cloud-based FSM solutions. This includes heavy-duty construction machinery (excavators, bulldozers, loaders), mining equipment (haul trucks, excavators, drills), agricultural machinery (tractors, harvesters, combines), and material handling equipment (forklifts, cranes). The common thread is the need for efficient management of a dispersed fleet of expensive, complex assets operating in challenging environments. The ability to remotely monitor equipment health, schedule maintenance proactively, and optimize operations is crucial for maximizing uptime and minimizing operational costs across these diverse applications.
Comparison of Aftermarket Cloud FSM Solutions
The following table compares the functionalities of three hypothetical leading aftermarket cloud FSM solutions (the names are illustrative and not representative of actual products). Real-world solutions offer a broader range of features and integrations, and specific functionalities vary considerably depending on vendor and pricing tiers.
Feature | Solution A | Solution B | Solution C |
---|---|---|---|
Real-time Equipment Tracking (GPS) | Yes, with geofencing | Yes, with route optimization | Yes, with live machine status integration |
Predictive Maintenance | Basic alerts based on hours of operation | Advanced analytics using sensor data | AI-driven predictions, integrating external data sources |
Remote Diagnostics | Limited diagnostic capabilities | Detailed fault code analysis | Comprehensive remote diagnostics with troubleshooting guides |
Work Order Management | Basic work order creation and tracking | Automated work order scheduling and dispatch | Integrated parts inventory management and technician scheduling |
Technological Advancements Driving Adoption
The off-highway equipment industry is undergoing a significant transformation, driven by rapid technological advancements. Cloud computing, the Internet of Things (IoT), big data analytics, mobile technologies, and artificial intelligence (AI) are converging to create a more efficient, data-driven, and proactive approach to fleet management and maintenance. This shift is fundamentally altering how aftermarket Field Service Management (FSM) systems operate, leading to increased uptime, reduced operational costs, and improved customer satisfaction.The integration of these technologies is revolutionizing aftermarket cloud FSM for off-highway equipment, fostering a paradigm shift from reactive to predictive maintenance strategies.
This proactive approach minimizes downtime, optimizes resource allocation, and improves overall equipment effectiveness.
Cloud Computing’s Role in Enhanced Off-Highway FSM
Cloud computing provides the foundational infrastructure for modern FSM systems. It allows for centralized data storage, accessible from anywhere with an internet connection. This eliminates the need for expensive on-premise servers and complex IT infrastructure, making the system scalable and cost-effective for businesses of all sizes. Furthermore, cloud-based systems offer enhanced data security through robust access controls and regular backups, mitigating the risk of data loss or breaches.
Companies like Caterpillar and John Deere are leveraging cloud platforms to manage vast amounts of equipment data, enabling better decision-making across their global operations.
The Impact of IoT and Big Data Analytics, Aftermarket cloud fsm offhighway
The Internet of Things (IoT) plays a crucial role by connecting off-highway equipment to the cloud, enabling real-time data collection on various parameters such as engine performance, fuel consumption, operational hours, and location. This data, often referred to as telematics data, is then analyzed using big data analytics techniques to identify trends, patterns, and anomalies that might indicate potential equipment failures.
For example, a sudden increase in engine temperature or vibration levels could be an early warning sign of a developing problem, allowing for proactive maintenance before a complete breakdown occurs. This predictive maintenance approach significantly reduces downtime and maintenance costs.
Mobile Technologies in Field Service Operations
Mobile technologies, such as tablets and smartphones, have transformed field service operations. Technicians can now access real-time equipment data, service manuals, and diagnostic information directly in the field, improving the efficiency and accuracy of repairs. Mobile FSM applications enable streamlined workflows, facilitating tasks like scheduling appointments, generating work orders, tracking parts inventory, and capturing digital signatures for completed service reports.
This enhances communication and collaboration between technicians, dispatchers, and customers, leading to faster response times and improved customer satisfaction. Imagine a scenario where a technician arrives on-site with all the necessary parts and information pre-loaded on their tablet, significantly reducing downtime.
AI and Machine Learning for Predictive Maintenance and Optimized Routing
AI and machine learning algorithms are being increasingly integrated into aftermarket cloud FSM systems to enhance predictive maintenance capabilities. By analyzing historical equipment data, operational patterns, and environmental factors, these algorithms can predict potential equipment failures with remarkable accuracy. This allows for proactive scheduling of maintenance, minimizing unexpected downtime and maximizing equipment availability. Furthermore, AI-powered route optimization tools analyze factors such as technician location, traffic conditions, and service priorities to create the most efficient routes, reducing travel time and improving overall field service efficiency.
A company could, for example, use machine learning to predict the likelihood of a specific component failing based on its usage patterns and environmental conditions, allowing for preventative replacement before a failure occurs.
Workflow of a Cloud-Based FSM System for Off-Highway Equipment Maintenance
A typical workflow for a cloud-based FSM system can be illustrated by the following flowchart:(Imagine a flowchart here. It would begin with “Equipment Sensor Data Transmission,” flowing to “Cloud Data Storage & Analysis,” then branching to “Predictive Maintenance Alerts” and “Technician Dispatch.” “Predictive Maintenance Alerts” would lead to “Preventative Maintenance Scheduling,” while “Technician Dispatch” would lead to “Mobile App Access to Work Order.” From there, it would proceed to “On-site Repair & Maintenance,” “Parts Ordering (if needed),” “Service Report Generation,” and finally, “Data Update in Cloud System.”) The flowchart depicts the seamless integration of data collection, analysis, and action, enabling proactive and efficient maintenance.
Benefits and Challenges of Cloud-Based FSM
The shift towards cloud-based Fleet Management Systems (FSM) is transforming the off-highway equipment industry, offering significant advantages in terms of efficiency and cost savings. However, this transition also presents challenges that need careful consideration before implementation. Understanding both the benefits and drawbacks is crucial for making informed decisions about adopting cloud-based FSM for your off-highway fleet.
Key Benefits of Cloud-Based FSM for Off-Highway Equipment
Cloud-based FSM offers several compelling advantages for off-highway equipment owners and operators. These systems provide real-time visibility into equipment performance, location, and maintenance needs, leading to improved operational efficiency and reduced downtime. The centralized nature of the data allows for better decision-making and proactive maintenance scheduling, minimizing costly unexpected repairs and maximizing equipment uptime. Furthermore, cloud-based solutions often integrate seamlessly with other business systems, improving overall workflow and data management.
Potential Challenges of Implementing and Managing a Cloud-Based FSM System
While the benefits are significant, implementing and managing a cloud-based FSM system presents certain challenges. Security is a primary concern; ensuring the confidentiality, integrity, and availability of sensitive equipment and operational data requires robust security measures, including encryption, access controls, and regular security audits. Data integration with existing systems can also be complex, requiring careful planning and potentially significant upfront investment.
Furthermore, reliance on a stable internet connection is essential for optimal functionality, and downtime due to connectivity issues can disrupt operations. Finally, choosing the right cloud provider and ensuring sufficient technical expertise within the organization are vital for successful implementation and ongoing management.
Total Cost of Ownership (TCO) Comparison: Cloud-Based vs. On-Premise FSM
Understanding the total cost of ownership is crucial when comparing cloud-based and on-premise FSM solutions. While initial setup costs might be higher for cloud-based systems due to software licensing and integration fees, the long-term operational costs are often lower.
- Cloud-Based FSM: Typically involves lower upfront hardware investment, reduced IT infrastructure maintenance costs, scalable pricing models based on usage, and potentially lower ongoing support costs.
- On-Premise FSM: Requires significant upfront investment in hardware, software licenses, and IT infrastructure. Ongoing maintenance, including server upgrades, security patches, and IT staff support, can be substantial.
The TCO of cloud-based systems often becomes more favorable over time, particularly for larger fleets or organizations with limited in-house IT resources. For example, a large mining company with hundreds of heavy equipment units might find that the scalability and reduced IT overhead of a cloud-based system significantly outweighs the initial investment.
Best Practices for Ensuring the Security and Reliability of Cloud-Based FSM Data
Protecting sensitive data within a cloud-based FSM system requires a proactive and multi-layered approach. This includes implementing robust security protocols such as data encryption both in transit and at rest, employing multi-factor authentication for user access, and regularly conducting security audits and penetration testing. Data backups and disaster recovery planning are also essential to ensure business continuity in case of unforeseen events.
Furthermore, selecting a reputable cloud provider with strong security certifications and compliance standards is paramount. Regular training for personnel on data security best practices and incident response procedures is crucial to minimize risks and maintain data integrity. Finally, keeping the FSM software updated with the latest security patches and features is essential for mitigating emerging threats.
Future Trends and Predictions
The aftermarket cloud FSM (Field Service Management) market for off-highway equipment is poised for significant growth over the next 5-10 years, driven by increasing connectivity, data-driven decision-making, and the demand for improved operational efficiency. We can expect to see a shift towards more integrated and intelligent solutions, leveraging emerging technologies to enhance maintenance and repair processes.The integration of advanced technologies will fundamentally reshape how off-highway equipment maintenance is managed.
This will translate into significant cost savings, reduced downtime, and improved overall equipment performance for businesses across various sectors.
Impact of Emerging Technologies
The adoption of blockchain technology offers the potential for enhanced security and transparency in managing service records and parts provenance. Imagine a system where every repair, part replacement, and maintenance activity is immutably recorded on a blockchain, creating an auditable trail that minimizes fraud and ensures the authenticity of parts. This would significantly improve trust and accountability within the supply chain.
Augmented reality (AR) will play a crucial role in facilitating remote diagnostics and guided repairs. Technicians equipped with AR headsets could receive real-time instructions overlaid onto their view of the equipment, allowing for faster and more accurate repairs, even in remote locations. This reduces the need for on-site expert visits, saving time and money.
Influence of Evolving Regulations and Industry Standards
Stringent environmental regulations and increasing focus on sustainability will drive the adoption of predictive maintenance solutions. Cloud-based FSM systems can analyze equipment data to predict potential failures, allowing for proactive maintenance and minimizing unplanned downtime. This not only reduces operational costs but also contributes to environmental sustainability by reducing fuel consumption and waste. Furthermore, standardization efforts within the off-highway equipment industry will lead to the development of interoperable FSM solutions, facilitating seamless data exchange between different equipment manufacturers and service providers.
This will improve efficiency and reduce integration complexities for businesses operating diverse fleets.
A Future Scenario for Off-Highway Equipment Maintenance
Imagine a scenario where a mining company’s haul truck experiences a sensor malfunction. The cloud-based FSM system, integrated with the truck’s onboard diagnostics, instantly detects the issue and alerts the maintenance team. Using AR technology, a remote technician guides an on-site mechanic through the repair process, providing real-time visual instructions and troubleshooting assistance. The entire process, from fault detection to resolution, is tracked and recorded on a secure blockchain, creating a transparent and auditable record.
The system also predicts the likelihood of future failures based on historical data and recommends proactive maintenance measures, ensuring optimal equipment uptime and minimizing costly downtime. The system automatically orders replacement parts, leveraging blockchain for secure and transparent supply chain management, ensuring genuine parts are used and delivered efficiently. This entire process is streamlined and optimized through the cloud-based FSM system, resulting in significant cost savings, improved efficiency, and enhanced equipment lifespan.
Case Studies of Successful Implementations
Successfully implementing aftermarket cloud FSM (Field Service Management) solutions in the off-highway equipment industry requires careful planning and execution. Several companies have achieved significant improvements in efficiency and customer satisfaction through strategic adoption of these technologies. The following case studies highlight best practices and demonstrate the tangible benefits of cloud-based FSM.
Case Study 1: XYZ Construction Equipment
XYZ Construction Equipment, a leading manufacturer of heavy-duty excavators and bulldozers, implemented a cloud-based FSM solution to streamline its service operations. Prior to implementation, their technicians relied on paper-based work orders and lacked real-time visibility into equipment location and maintenance history. The new system integrated with their existing ERP and CRM systems, providing technicians with access to comprehensive equipment data, customer information, and scheduling tools directly on their mobile devices.
This allowed for faster response times, reduced downtime, and improved inventory management.
Case Study 2: ABC Agricultural Machinery
ABC Agricultural Machinery, a global provider of tractors and harvesting equipment, faced challenges in managing a large and geographically dispersed service network. Their previous system was inefficient, resulting in scheduling conflicts, delayed repairs, and dissatisfied customers. By adopting a cloud-based FSM solution, ABC Agricultural Machinery improved technician dispatching, optimized route planning, and gained real-time insights into service operations. The company saw significant improvements in first-time fix rates and overall customer satisfaction.
A key factor in their success was the comprehensive training provided to their technicians and service managers.
Case Study 3: DEF Mining Equipment
DEF Mining Equipment, a manufacturer of large-scale mining machinery, required a robust and reliable FSM solution to manage the complex maintenance requirements of their equipment. The company’s previous system was unable to handle the large volume of data and the diverse range of equipment types. Their cloud-based FSM solution addressed these challenges by providing a centralized platform for managing all aspects of service operations, from scheduling and dispatching to parts inventory and reporting.
This resulted in improved equipment uptime, reduced maintenance costs, and enhanced safety. Overcoming initial resistance to adopting new technology within the workforce was a significant hurdle, but a phased rollout and targeted training addressed this.
Successful Implementation Factors and Challenges
Company Name | Equipment Type | Benefits Achieved | Challenges Faced |
---|---|---|---|
XYZ Construction Equipment | Excavators, Bulldozers | Faster response times, reduced downtime, improved inventory management | Initial integration complexities with existing systems |
ABC Agricultural Machinery | Tractors, Harvesting Equipment | Improved technician dispatching, optimized route planning, increased first-time fix rates | Training technicians on new software and processes |
DEF Mining Equipment | Large-scale Mining Machinery | Improved equipment uptime, reduced maintenance costs, enhanced safety | Overcoming resistance to adopting new technology |
Outcome Summary
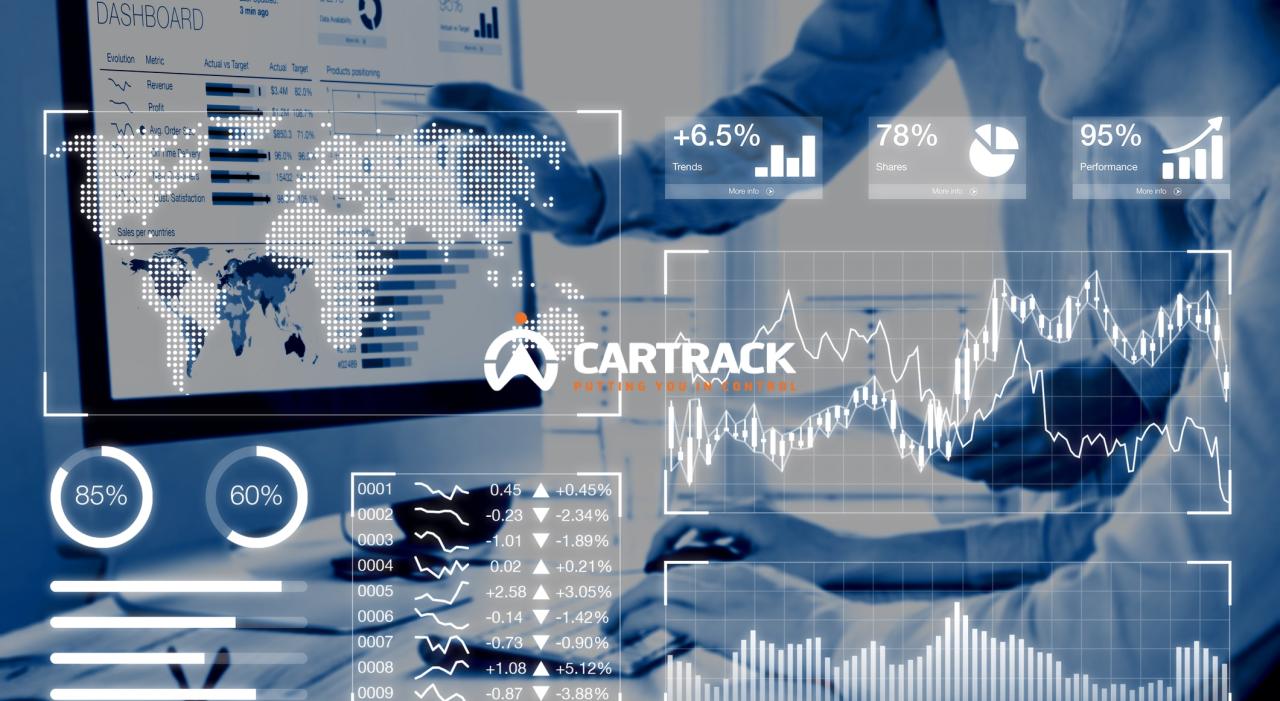
From optimizing maintenance schedules and reducing downtime to enhancing technician efficiency and improving overall profitability, the benefits of aftermarket cloud FSM for off-highway equipment are undeniable. While challenges exist, the innovative technology behind it, coupled with industry best practices, is paving the way for a future where maintenance is smarter, more efficient, and ultimately, more cost-effective. The journey towards fully optimized fleet management is underway, and the cloud is leading the charge.
Clarifying Questions
What is the typical cost of implementing an aftermarket cloud FSM solution?
Costs vary significantly depending on the scale of your operation, the chosen software provider, and the specific features required. It’s best to request quotes from several vendors to compare pricing and features.
How secure is my data in a cloud-based FSM system?
Reputable providers employ robust security measures, including encryption, access controls, and regular security audits. However, it’s crucial to thoroughly vet any provider and understand their security protocols before committing.
What level of technical expertise is needed to use a cloud-based FSM system?
Most modern systems are designed with user-friendliness in mind. While some initial training might be necessary, many platforms offer intuitive interfaces and readily available support resources.
Can a cloud-based FSM system integrate with my existing systems?
Ideally, yes. Many systems offer API integrations to connect with other software applications, such as ERP or CRM systems. However, the level of integration will depend on the specific software involved.