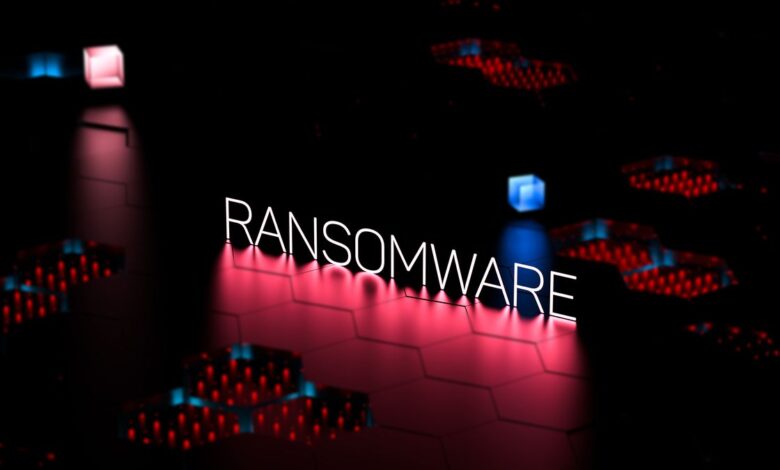
Meet the Ransomware Gang That Demands $500 Million
Meet the ransomware gang that demands 500 million – Meet the ransomware gang that demands $500 million – a staggering sum that highlights the escalating threat of cybercrime. This isn’t your average script kiddie operation; we’re talking about a sophisticated, well-organized group capable of crippling businesses and institutions worldwide. Their audacity in demanding such a massive ransom raises serious questions about their resources, capabilities, and ultimate goals.
This post dives deep into their profile, their methods, and the chilling implications of their actions.
We’ll explore their operational structure, examining their attack vectors and the potential geographic locations they operate from. We’ll analyze the $500 million demand itself, comparing it to previous ransomware attacks and speculating on the motivations behind such a bold move. We’ll also look at the devastating impact on victims, both financially and reputationally, and discuss strategies for mitigation and prevention.
Finally, we’ll examine the challenges law enforcement faces in combating these cybercriminals and the crucial role of international cooperation.
The Ransomware Gang
This blog post delves into the profile and operations of a recently active ransomware gang responsible for a $500 million demand. While specific details about the gang remain shrouded in secrecy, piecing together available information allows us to paint a picture of their methods, targets, and likely origins. This analysis aims to provide insight into their modus operandi and the potential threat they represent.
Operational Structure
The gang’s operational structure is likely decentralized, employing a tiered system. This structure involves a core group of developers responsible for creating and maintaining the ransomware, a network of affiliates who deploy the malware, and potentially a money laundering operation to handle the ransom payments. This decentralized approach makes it harder to identify and disrupt the entire operation, as the takedown of one affiliate doesn’t necessarily cripple the whole enterprise.
The communication between these tiers is likely encrypted and conducted through anonymous channels like dark web forums or encrypted messaging apps.
Methods of Attack and Infiltration
The gang likely utilizes a multi-pronged approach to infiltration, combining phishing campaigns with sophisticated exploits targeting known vulnerabilities in software and operating systems. Initial access is often gained through spear-phishing emails containing malicious attachments or links leading to compromised websites. Once inside a network, the ransomware spreads laterally, encrypting critical data and systems. The gang may also employ techniques like double extortion, threatening to leak stolen data if the ransom isn’t paid.
They likely leverage readily available exploit kits and custom-built malware to enhance their success rate.
Geographic Location and Resources
Pinpointing the gang’s precise geographic location is challenging. However, based on language used in communications and previous attack patterns, a location in Eastern Europe or Russia is a strong possibility. This region has historically been a hub for cybercriminal activity, offering a combination of technical expertise, relaxed law enforcement, and a less-stringent regulatory environment. The gang’s ability to demand such a large sum suggests access to significant resources and a high level of organizational capability.
History and Previous Attacks
Information on the gang’s past activities is limited, likely due to their operational security. However, the sophistication of their current attack and the size of their demand indicate previous successful ransomware operations. They likely started with smaller targets, gradually increasing their ambitions and capabilities over time. The $500 million demand represents a significant escalation, highlighting their growing confidence and operational reach.
Attribution to specific past attacks is difficult without concrete evidence, but analysis of the ransomware code and attack techniques may reveal links to previous incidents.
Key Characteristics of the Gang
Name | Method | Target | Demand |
---|---|---|---|
(Unknown – Referenced as “Gang X”) | Spear-phishing, Exploits, Lateral Movement, Double Extortion | Large Corporations, Critical Infrastructure (Potential) | $500,000,000 |
The $500 Million Demand: Meet The Ransomware Gang That Demands 500 Million
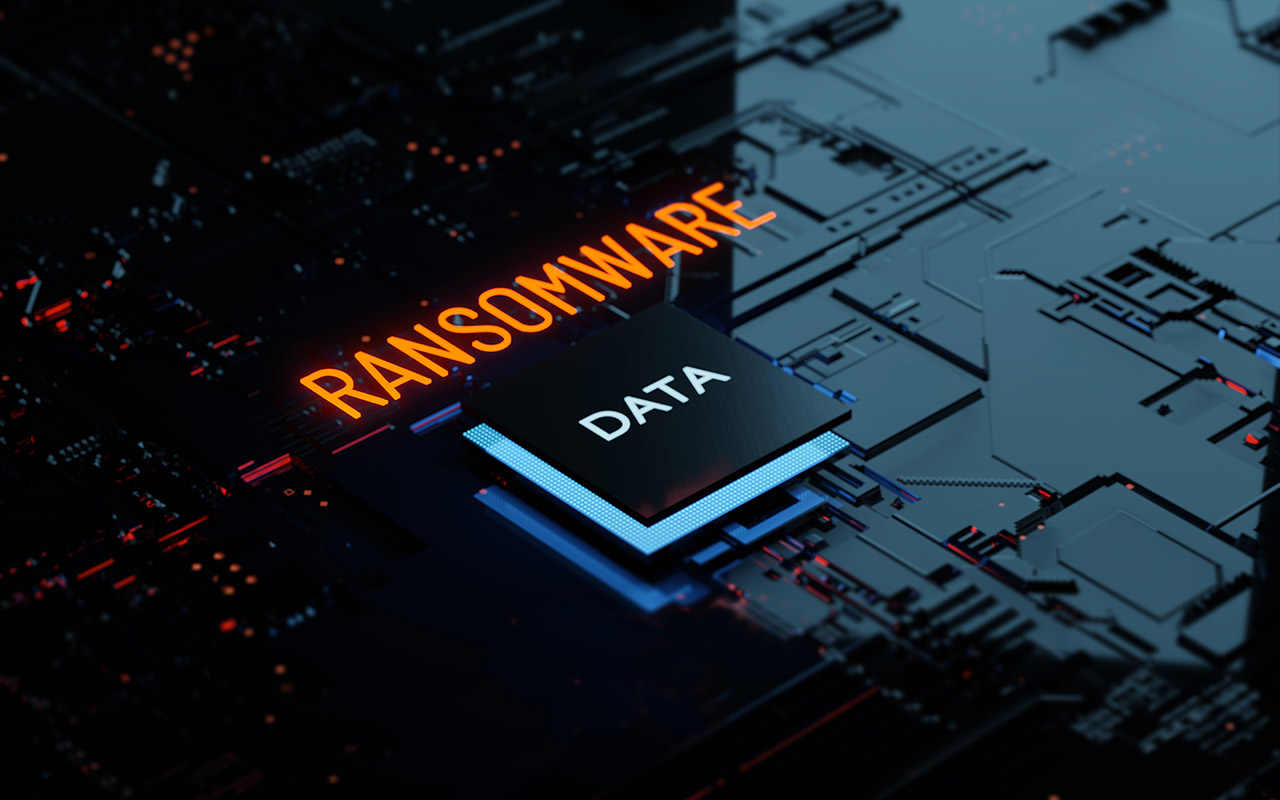
A half-billion-dollar ransom demand is unprecedented in the world of ransomware attacks. This staggering figure immediately catapults this incident into the realm of the most significant cyber extortion events in history, demanding a closer examination of its context, implications, and potential ramifications. The sheer scale of the demand raises questions about the capabilities and ambitions of the perpetrators, and the vulnerabilities of their target.The Significance of the $500 Million Ransom Demand in the Context of Other Ransomware AttacksThis $500 million demand dwarfs previous high-profile ransomware attacks.
While attacks targeting major corporations have resulted in multi-million dollar payouts, the jump to a half-billion represents a significant escalation. Previous record-breaking ransomware demands, though substantial, pale in comparison. For example, the Colonial Pipeline attack in 2021 resulted in a payment of approximately $4.4 million, highlighting the extraordinary scale of this new threat. This leap suggests a shift in the ransomware landscape, possibly indicating the emergence of more sophisticated and ambitious criminal groups with access to extensive resources and intelligence.
Comparison to Previous High-Value Ransom Requests
A comparison with previous high-profile attacks reveals a clear upward trend. While attacks like the NotPetya attack in 2017 caused billions of dollars in damages, the ransom demands themselves remained comparatively lower. The recent increase in ransom demands correlates with the increasing sophistication of ransomware techniques, including the use of double extortion tactics (data encryption and data exfiltration) and the targeting of high-value assets within critical infrastructure sectors.
This $500 million demand underscores a potential new paradigm where the financial stakes are exponentially higher.
Potential Motivations Behind Such a Large Demand
Several factors could motivate such a massive ransom demand. The attackers likely possess highly sensitive data, the loss or exposure of which could inflict catastrophic financial and reputational damage on the victim. This could include intellectual property, customer data, or critical operational information. The attackers might also be leveraging the victim’s dependence on their systems and the potential disruption caused by a prolonged outage.
The sheer size of the demand may also be a strategic move to deter law enforcement intervention and maximize their chances of a successful payout. Furthermore, the attackers might be operating under the assumption that a large corporation or government entity might be more willing to pay a large sum to avoid the significant negative consequences of a data breach or system shutdown.
Likely Targets of This Attack
Given the scale of the demand, the target is likely a large multinational corporation or a critical infrastructure provider. Companies in the finance, energy, healthcare, or technology sectors are prime candidates, as they possess vast amounts of valuable data and rely heavily on operational continuity. A government agency, especially one responsible for essential services, is another plausible target.
The attackers are likely to have meticulously researched their target, identifying its vulnerabilities and the potential impact of a successful attack. The choice of target is clearly calculated to maximize the potential payout and minimize the risk of detection and apprehension.
Hypothetical Scenario: Ransom Money Usage
If the ransom is paid, the gang might utilize a multi-pronged approach to laundering the money. Initially, they could move the funds through a series of cryptocurrency exchanges, using mixers or tumblers to obscure the trail. Subsequently, they could convert the cryptocurrency into fiat currency through various channels, potentially involving shell companies and offshore accounts. A portion of the funds might be used to invest in other criminal activities, such as purchasing more sophisticated hacking tools or recruiting new members.
Another portion might be used to fund lavish lifestyles, acquiring luxury goods and properties under false identities. Finally, some funds could be strategically distributed among the gang members to ensure loyalty and prevent internal conflicts. This complex and carefully orchestrated process aims to make tracing the funds extremely difficult.
Victim Impact and Response
Paying a ransom to a ransomware gang, even one demanding a staggering $500 million, doesn’t guarantee data recovery or prevent future attacks. Victims often find themselves in a precarious situation, facing significant financial, legal, and reputational damage regardless of their decision. Understanding the potential consequences and implementing proactive measures is crucial for minimizing the long-term impact.The potential impact on victims who pay the ransom is multifaceted and often far-reaching.
While paying might seem like the quickest solution to restore operations, it doesn’t guarantee data recovery. Ransomware gangs are not always trustworthy, and even after payment, victims may find their data remains encrypted or is destroyed. Furthermore, paying the ransom encourages future attacks, effectively rewarding criminal behavior and potentially fueling more sophisticated and widespread ransomware campaigns. The financial burden of the ransom itself, combined with the costs of recovery, legal fees, and potential business disruption, can be crippling, especially for smaller organizations.
The incident can lead to loss of customers, damage to brand reputation, and ultimately, business failure. Consider the case of Colonial Pipeline, which paid a multi-million dollar ransom in 2021; while they regained access to their systems, the reputational damage and the financial strain of the incident were substantial.
Legal and Reputational Consequences for Victims
Paying a ransom can have serious legal ramifications. In some jurisdictions, paying ransoms is illegal, potentially leading to fines or other penalties. Furthermore, victims may face scrutiny from regulatory bodies, particularly if the attack involves sensitive personal data or financial information, triggering investigations under regulations like GDPR or CCPA. The reputational damage from a ransomware attack can be devastating, impacting customer trust, investor confidence, and overall brand value.
A public association with a ransomware attack can lead to significant loss of business, impacting revenue and market share. The impact is amplified when the victim is a large organization or a public entity.
Strategies to Mitigate Damage from a Ransomware Attack
Mitigating the damage from a ransomware attack requires a multi-pronged approach. Proactive measures, such as regular data backups, robust cybersecurity protocols, employee training on phishing and social engineering tactics, and the implementation of multi-factor authentication, are essential. These measures significantly reduce the impact of a successful attack. In the event of an attack, a swift and organized response is crucial.
This includes isolating affected systems to prevent further spread, engaging cybersecurity experts for incident response, and thoroughly assessing the extent of the breach. A well-defined incident response plan can significantly minimize downtime and data loss. Remember, a successful recovery plan relies on meticulous planning and regular testing.
Reporting the Incident to Law Enforcement
Reporting a ransomware attack to law enforcement is crucial. Law enforcement agencies, such as the FBI’s Internet Crime Complaint Center (IC3), have dedicated units to investigate cybercrimes and can provide valuable assistance in tracing the attackers and potentially recovering data. Providing law enforcement with detailed information about the attack, including any ransom demands or communication with the attackers, is essential for effective investigation.
Early reporting can also facilitate coordination with other victims and contribute to broader efforts to combat ransomware.
Resources Available to Victims of Ransomware Attacks
Victims of ransomware attacks can access several resources to help them navigate the challenging aftermath. These include:
- The FBI’s Internet Crime Complaint Center (IC3): Provides a platform for reporting cybercrimes and offers guidance on handling ransomware incidents.
- The Cybersecurity and Infrastructure Security Agency (CISA): Offers resources, alerts, and guidance on cybersecurity best practices and incident response.
- Private cybersecurity firms: Specialize in incident response and can provide expert assistance in recovering data, investigating the attack, and mitigating the damage.
- Legal counsel: Can advise on legal implications, regulatory compliance, and potential litigation.
- Insurance providers: Cybersecurity insurance policies can cover some of the costs associated with ransomware attacks, including ransom payments (though this is often subject to policy limitations), data recovery, and legal fees.
Law Enforcement and Countermeasures
Bringing down a ransomware gang demanding $500 million isn’t a simple task. It requires a multi-faceted approach involving international cooperation, advanced technological solutions, and persistent investigative work. Law enforcement faces significant hurdles, but effective strategies exist to disrupt these criminal enterprises.The challenges law enforcement faces are numerous. Ransomware gangs often operate from countries with weak legal frameworks or lack of extradition treaties, making prosecution difficult.
They utilize sophisticated techniques to obfuscate their activities, including using encrypted communications, anonymizing networks like Tor, and employing cryptocurrency for untraceable payments. Attribution of attacks to specific individuals or groups can also be incredibly complex, requiring extensive digital forensics and intelligence gathering. Furthermore, the decentralized and constantly evolving nature of these groups makes targeting them challenging; dismantling one cell often leads to another emerging.
Hearing about that ransomware gang demanding $500 million got me thinking about security vulnerabilities in general. Building robust, secure applications is crucial, and that’s where understanding the future of app development comes in. Check out this article on domino app dev the low code and pro code future to see how we can improve our defenses. Ultimately, the fight against ransomware hinges on creating more secure systems, so learning about innovative development practices is key.
Challenges in Investigating and Prosecuting Ransomware Gangs
Investigating and prosecuting ransomware gangs presents significant obstacles. Jurisdictional issues arise when victims and perpetrators are located in different countries, hindering the smooth flow of information and evidence sharing. The use of cryptocurrency and anonymous online platforms complicates tracing funds and identifying individuals involved in the attacks. The sophisticated techniques used by these gangs, including the use of malware variants and ever-changing infrastructure, require specialized expertise and resources from law enforcement agencies.
Finally, the lack of global standardized legal frameworks and cooperation mechanisms often hampers the effectiveness of international efforts to combat ransomware.
Effective Strategies for Disrupting Ransomware Operations
Effective strategies involve a multi-pronged approach. Proactive measures such as strengthening cybersecurity infrastructure and educating individuals and organizations about best practices are crucial in preventing attacks. Law enforcement can use intelligence gathering to identify and target key members of ransomware gangs, disrupting their operations and seizing assets. This often involves collaborative efforts with private sector cybersecurity firms, sharing threat intelligence and working together to identify vulnerabilities.
Successful operations rely on proactive infiltration of these groups, tracking their communication channels, and identifying their infrastructure, leading to arrests and the seizure of cryptocurrency wallets.
Technological Solutions for Preventing Ransomware Attacks
Technological solutions are paramount. Robust endpoint detection and response (EDR) systems can identify and contain ransomware infections before they spread. Regular software patching and updates are essential to close security vulnerabilities exploited by ransomware. Multi-factor authentication (MFA) adds an extra layer of security, making it harder for attackers to access systems. Data backups, regularly tested and stored offline, are crucial for data recovery in case of an attack.
Employing a zero trust security model, which assumes no implicit trust, limits the impact of a successful breach. Finally, sandboxing and threat intelligence platforms help analyze suspicious files and proactively identify malicious activity.
The Role of International Cooperation in Combating Ransomware
International cooperation is critical. Sharing intelligence and coordinating law enforcement actions across borders are essential for effectively targeting globally operating ransomware gangs. Harmonizing legal frameworks and establishing mutual legal assistance treaties can streamline the process of extraditing suspects and seizing assets. International organizations, such as Interpol and Europol, play a vital role in facilitating cooperation and sharing best practices.
Joint operations, involving multiple countries’ law enforcement agencies, can lead to significant disruptions of ransomware networks and arrests of key players. The development of shared databases of threat intelligence and malware samples further strengthens collective efforts.
Hypothetical Successful Law Enforcement Operation
Imagine a coordinated international operation targeting the “DarkWeb Devils” ransomware gang. Through intelligence gathered from various sources, including undercover operations and analysis of encrypted communications, law enforcement identifies key servers and communication channels used by the gang. Simultaneous raids in several countries, coordinated through Interpol, lead to the arrest of key members, including the group’s leader and several programmers.
The operation results in the seizure of millions of dollars in cryptocurrency, the dismantling of the gang’s infrastructure, and the recovery of stolen data. This coordinated effort demonstrates the power of international cooperation in disrupting sophisticated ransomware operations and bringing criminals to justice.
Illustrative Examples
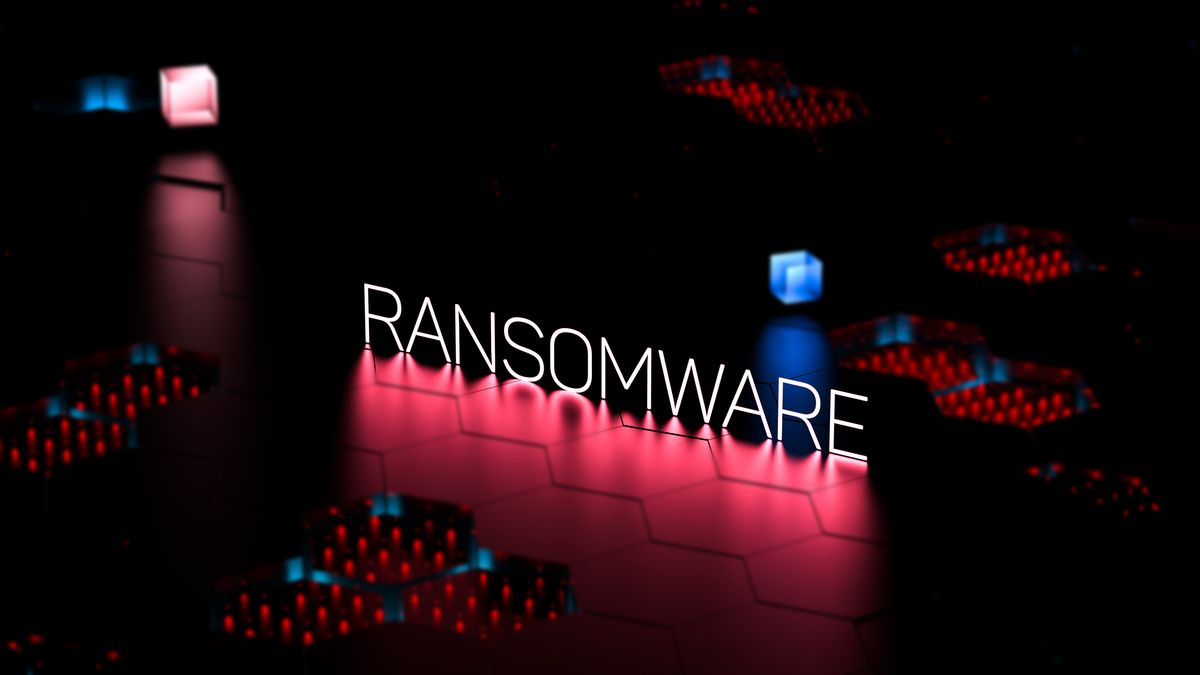
To better understand the devastating impact of a $500 million ransomware attack, let’s examine a hypothetical scenario and explore the technical aspects of such an operation. This will provide a clearer picture of the complexities involved and the scale of the threat.
Hypothetical Victim Company: GlobalTech Industries
GlobalTech Industries, a multinational corporation specializing in cloud-based software solutions, suffered a crippling ransomware attack. Their sophisticated network, spanning multiple continents and housing sensitive customer data, became the target of a highly organized ransomware gang. The attack resulted in the encryption of critical databases, halting all operations, including customer support, software development, and billing systems. The immediate impact included significant financial losses due to operational downtime, reputational damage leading to customer churn, and the potential for hefty legal penalties for data breaches.
The long-term consequences included a substantial investment in cybersecurity upgrades, recovery efforts, and the potential for long-term loss of market share. The sheer volume of encrypted data made recovery incredibly challenging and expensive, leading them to consider paying the ransom despite the risks.
Ransomware Gang’s Network Infrastructure
The ransomware gang likely operates a distributed network infrastructure, employing various techniques to maintain anonymity and evade detection. A simplified text-based representation could look like this:“` Command & Control Server (C&C)
[Encrypted, Multi-Layered]
| | Encrypted Communication Channels V Botnet (compromised machines globally)
[Decentralized, constantly shifting IPs]
| | Data Exfiltration & Ransomware Deployment V Victim Networks (GlobalTech Industries)
[Multiple locations]
“`This illustration highlights the distributed nature of the infrastructure. The C&C server is heavily protected, while the botnet provides a large pool of compromised machines to launch attacks and exfiltrate data. The constant shifting of IP addresses and encrypted communication channels make tracking the gang extremely difficult.
Hypothetical Ransom Payment Flow
The payment process, if GlobalTech decided to pay, would likely involve multiple layers of obfuscation to protect the gang’s identity and financial trail.
1. Initial Contact
GlobalTech receives a ransom demand via encrypted communication channels.
2. Negotiation
A complex negotiation process begins, possibly involving a third-party intermediary.
3. Payment Method
The ransom is likely paid using untraceable cryptocurrencies like Bitcoin, through multiple layered transactions to obscure the origin.
4. Decryption Key Transfer
Once the ransom is confirmed, the decryption key is provided, ideally through another encrypted channel.
5. Verification
GlobalTech verifies the key’s functionality and restores a portion of their data.This process is designed to be as anonymous as possible, making tracing the funds and identifying the perpetrators extremely challenging. The use of cryptocurrencies, mixers, and multiple layers of transactions would make tracking extremely difficult. The success of law enforcement in tracing these funds has been historically low.
Data Encryption and Decryption Process, Meet the ransomware gang that demands 500 million
The ransomware gang likely uses sophisticated encryption algorithms, such as AES-256 or RSA, to encrypt GlobalTech’s data. The process typically involves:
1. File Selection
The ransomware scans the victim’s network, identifying and selecting target files based on file extensions or other criteria.
2. Encryption
A strong encryption algorithm is used to encrypt each selected file, rendering it inaccessible. A unique encryption key is often generated for each file or a group of files.
3. Ransom Note
A ransom note is left, detailing the attack and providing instructions for payment.
4. Decryption (Post-Payment)
After receiving the ransom, the gang provides a decryption key or a decryption tool that reverses the encryption process, restoring access to the files.The sophistication of the encryption algorithm and the use of unique keys per file make decryption extremely difficult without the correct key, highlighting the critical importance of robust backups and data recovery strategies. The complexity of the encryption process also makes it very difficult for law enforcement to decrypt the data without the gang’s cooperation.
End of Discussion
The $500 million ransomware demand isn’t just a number; it’s a stark warning about the evolving landscape of cybercrime. This highly organized gang presents a significant threat, demanding resources and expertise far beyond typical ransomware operations. Understanding their methods, motivations, and the devastating impact on victims is crucial for both individuals and organizations to bolster their defenses. While law enforcement faces significant hurdles, international collaboration and technological advancements offer hope in the fight against these digital criminals.
The future of cybersecurity depends on our collective ability to stay ahead of these evolving threats.
Common Queries
What kind of organizations are most likely to be targeted by this gang?
Likely targets include large corporations with valuable data, government entities holding sensitive information, and organizations in critical infrastructure sectors.
What happens if a victim refuses to pay the ransom?
Refusal to pay typically results in the permanent loss of data, significant operational disruption, and potentially reputational damage.
Are there any guarantees that paying the ransom will lead to data recovery?
There’s no guarantee. Even after payment, there’s no assurance the gang will provide the decryption key, leaving victims with significant losses.
What steps can individuals take to protect themselves from ransomware attacks?
Regularly update software, use strong passwords, back up data regularly, and be wary of suspicious emails and links.