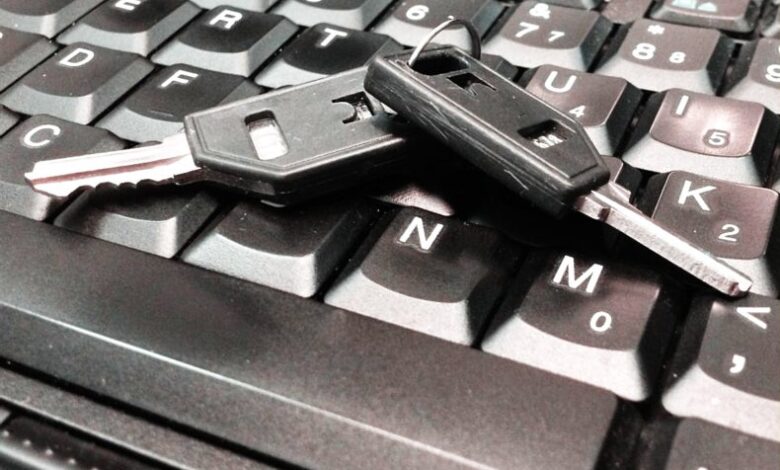
Network Connected Wrenches Now Vulnerable to Ransomware
Network connected wrenches are now vulnerable to ransomware attacks – a chilling reality for the industrial internet of things (IIoT). Imagine this: your entire factory floor, its intricate assembly lines reliant on precisely controlled robotic arms, brought to a grinding halt by a malicious software attack targeting the seemingly innocuous network-connected wrenches. This isn’t science fiction; it’s a growing threat, and understanding the vulnerabilities, potential consequences, and preventative measures is crucial for safeguarding our increasingly interconnected industrial world.
The implications are far-reaching, affecting productivity, safety, and even national security in certain sectors.
The vulnerabilities stem from several factors, including outdated firmware, weak authentication protocols, and a lack of robust security measures on these seemingly simple devices. Attackers can exploit these weaknesses to gain unauthorized access, encrypt critical data, and demand ransom payments to restore functionality. The consequences can range from minor production delays to catastrophic system failures, resulting in significant financial losses, reputational damage, and potential safety hazards.
Different ransomware strains, specifically designed to target industrial control systems (ICS), pose an even greater threat, capable of causing widespread disruption and chaos.
The Threat Landscape
The rise of the Internet of Things (IoT) has brought unprecedented connectivity to various aspects of our lives, including industrial settings. While this connectivity offers benefits in terms of efficiency and monitoring, it also introduces new vulnerabilities, particularly to ransomware attacks. Networked wrenches, seemingly innocuous tools, are now part of this interconnected landscape, and their susceptibility to ransomware poses a significant threat to industrial operations.The vulnerabilities of network-connected wrenches stem from their integration into larger industrial control systems (ICS).
These systems often lack the robust security measures found in traditional IT networks, making them easier targets for malicious actors. Furthermore, many industrial devices, including networked wrenches, operate on outdated software and lack essential security updates, exacerbating the vulnerability. A compromised wrench could serve as an entry point into the broader ICS, potentially leading to widespread disruption.
Seriously, ransomware is getting out of hand! Now even network-connected wrenches are targets. It makes you wonder about the security implications of increasingly connected devices, especially when you consider the rapid development of applications. Learning more about secure app development is crucial, like exploring the possibilities in domino app dev the low code and pro code future , which could help us build more resilient systems.
The fact that even simple tools are now vulnerable highlights the urgent need for better security practices across the board.
Vulnerabilities of Networked Wrenches to Ransomware
Networked wrenches, typically used for precise torque control in manufacturing or assembly lines, often communicate with central control systems via various protocols, such as Modbus or Profibus. These protocols, while efficient for data transmission, may lack built-in security features, leaving them susceptible to various attacks. A compromised wrench could be manipulated to send incorrect torque values, leading to faulty assembly or even equipment damage.
More critically, it could serve as a stepping stone for lateral movement within the ICS, granting attackers access to more critical systems. The lack of regular security patching and updates on these devices, often due to concerns about downtime, creates significant opportunities for exploitation.
Potential Consequences of a Ransomware Attack
A successful ransomware attack on a network of wrenches could have far-reaching consequences. The immediate impact could involve the disruption of production lines, leading to significant financial losses due to downtime and lost output. Beyond the direct financial losses, reputational damage can also occur, especially if the attack leads to product recalls or safety incidents. The recovery process can be lengthy and expensive, involving forensic analysis, system restoration, and potential legal ramifications.
In scenarios involving critical infrastructure, a ransomware attack on networked tools could even lead to safety hazards and public health risks. For example, a compromised wrench in a pharmaceutical manufacturing plant could result in compromised product quality or safety, with potentially devastating consequences.
Attack Vectors for Compromising Networked Wrenches, Network connected wrenches are now vulnerable to ransomware attacks
Several attack vectors could be exploited to compromise networked wrenches. These include: malware infections through phishing emails or infected USB drives, exploiting vulnerabilities in the wrench’s firmware or communication protocols, and gaining access through unsecured network connections. Attackers could also leverage compromised credentials or weak passwords to gain unauthorized access. Finally, social engineering tactics could be used to trick employees into providing access or revealing sensitive information.
Examples of Ransomware Targeting Industrial Control Systems
Several ransomware strains have been known to target industrial control systems, including those potentially impacting wrench networks. While specific examples targeting wrenches directly are rare due to the sensitive nature of such attacks, ransomware like Industroyer, Triton, and NotPetya have demonstrated the potential for widespread disruption within ICS environments. These attacks highlight the ability of ransomware to not only encrypt data but also to directly manipulate industrial processes, causing significant physical damage or operational disruptions.
The impact of such attacks on a network of wrenches could range from simple operational disruptions to catastrophic failures depending on the nature of the targeted system and the sophistication of the attack.
Ransomware Protection Strategies for Industrial Networks
The following table compares different ransomware protection strategies for industrial networks:
Strategy | Implementation Cost | Effectiveness | Potential Downside |
---|---|---|---|
Network Segmentation | Medium to High | High | Increased complexity, potential for performance impact |
Regular Security Patching | Low to Medium | Medium to High | Potential for downtime during patching |
Intrusion Detection/Prevention Systems (IDS/IPS) | Medium to High | Medium to High | False positives, potential for performance impact |
Regular Backups and Disaster Recovery Planning | Low to Medium | High | Requires robust storage and testing of recovery procedures |
Employee Security Awareness Training | Low | Medium | Requires ongoing reinforcement and updates |
Microsegmentation | High | High | Complex implementation and management |
Security Protocols and Best Practices
The recent vulnerability of network-connected wrenches to ransomware highlights a critical need for robust security protocols within Industrial IoT (IIoT) environments. Ignoring these vulnerabilities leaves manufacturers exposed to significant financial losses, operational downtime, and reputational damage. Implementing comprehensive security measures is no longer optional; it’s a necessity for maintaining operational integrity and protecting valuable assets.The security of industrial networks, particularly those involving devices like network-connected wrenches, demands a multi-layered approach.
This goes beyond simple antivirus software and requires a deep understanding of the potential attack vectors and vulnerabilities specific to IIoT devices. A proactive strategy is crucial, focusing on prevention and rapid response to minimize the impact of any successful attack.
Network Segmentation and Access Control
Network segmentation is a fundamental security practice that divides a network into smaller, isolated segments. This limits the impact of a ransomware attack by preventing it from spreading rapidly throughout the entire network. If a wrench on one segment is compromised, the ransomware will be contained within that segment, preventing it from infecting other critical systems like manufacturing control systems or enterprise networks.
Access control mechanisms, such as role-based access control (RBAC), further restrict access to sensitive data and resources. This ensures that only authorized personnel can access and modify critical network components and wrench configurations, minimizing the risk of malicious actions. Implementing strong passwords and multi-factor authentication (MFA) adds another layer of protection, making it significantly harder for attackers to gain unauthorized access.
Essential Security Features for Network-Connected Wrenches
Several key security features are essential for protecting network-connected wrenches. Firmware updates are crucial for patching security vulnerabilities that attackers might exploit. Regular and timely updates are essential to maintain a strong security posture. Strong authentication mechanisms, including MFA, are vital to prevent unauthorized access to the wrenches and their associated data. Encryption, both in transit and at rest, protects sensitive data from unauthorized access, even if the wrench is compromised.
Data encryption ensures that even if the data is stolen, it remains unreadable without the decryption key. Finally, regular security audits and vulnerability assessments are critical for identifying and addressing potential weaknesses in the wrench’s security configuration.
Hypothetical Security Architecture for a Network of Wrenches
A secure network of wrenches requires a carefully designed architecture. The architecture would begin with a dedicated, segmented network for the wrenches, isolated from other critical systems. Each wrench would be equipped with a secure boot process and strong authentication mechanisms. All communication between the wrenches and the central management system would be encrypted using a robust protocol like TLS 1.3.
The central management system would have its own robust security measures in place, including firewalls, intrusion detection systems, and regular security audits. A system for detecting and responding to anomalies, such as unusual access patterns or data transfers, would be implemented to provide early warning of potential attacks. Furthermore, a robust incident response plan would be in place to quickly contain and mitigate any security breaches.
This plan would include procedures for isolating compromised wrenches, restoring data from backups, and investigating the root cause of the breach. Regular security awareness training for personnel involved in managing and maintaining the wrench network would also be critical.
Incident Response and Recovery
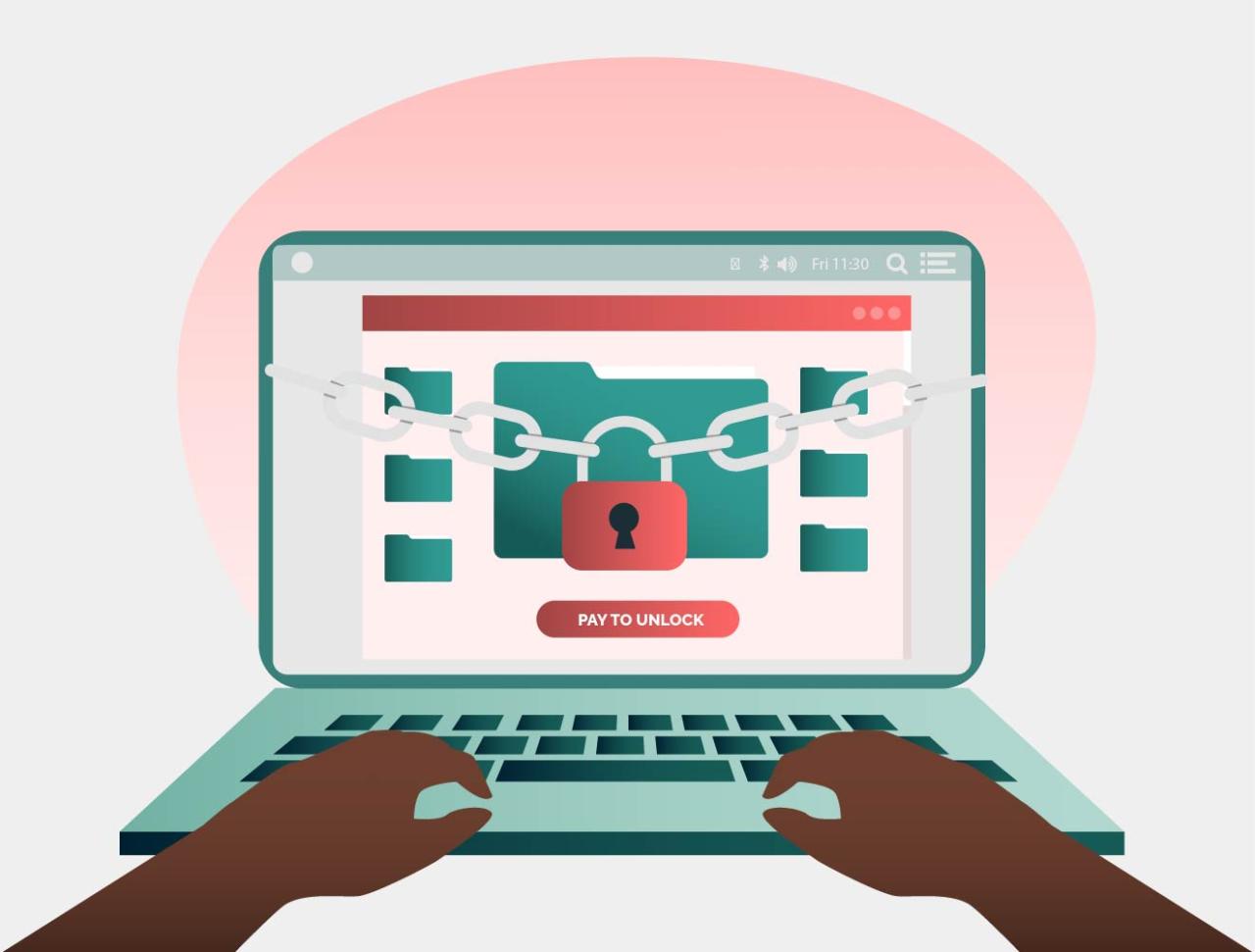
A ransomware attack on a network of connected wrenches, while seemingly improbable, highlights the expanding reach of cyber threats. The interconnected nature of modern industrial systems, even seemingly simple tools, makes them vulnerable. A swift and effective response is crucial to minimize damage and restore operations. This section Artikels a step-by-step procedure for handling such an incident.
Incident Response Procedure
Responding to a ransomware attack requires a structured approach. The speed and effectiveness of your response directly correlate with the extent of the damage and the cost of recovery. First, isolate affected devices from the network to prevent further spread. Then, thoroughly assess the extent of the compromise, identifying infected wrenches and the type of ransomware involved. Next, create a detailed record of all affected systems and the actions taken.
This documentation is vital for recovery and future security improvements. Finally, initiate data recovery and system remediation, following established protocols and best practices.
Effective Incident Response Strategies
Minimizing the impact of a ransomware attack necessitates proactive measures. Regular security audits and vulnerability assessments can identify weaknesses before they are exploited. Employing strong passwords and multi-factor authentication enhances security. Keeping software updated and patched protects against known vulnerabilities. Implementing a robust intrusion detection system (IDS) and an intrusion prevention system (IPS) helps identify and block malicious activity in real-time.
Regular security awareness training for personnel involved in managing the wrench network is also essential. For example, training could cover identifying phishing emails and practicing safe internet browsing habits.
Data Restoration and System Remediation
Data restoration is a critical part of the recovery process. This process begins with restoring data from backups. Ideally, these backups should be stored offline and regularly tested to ensure their integrity and recoverability. If backups are unavailable or compromised, specialized data recovery tools might be necessary. System remediation involves cleaning and reinstalling operating systems on affected wrenches, ensuring all malicious software is removed.
After remediation, rigorous testing is necessary to verify system stability and security before reconnecting to the network. This might involve running malware scans and vulnerability assessments to ensure no remnants of the ransomware remain.
Importance of Backups and Disaster Recovery Planning
Regular backups and a comprehensive disaster recovery plan are fundamental to mitigating the effects of a ransomware attack. Backups should be made frequently and stored securely, ideally in multiple locations, using the 3-2-1 backup rule (3 copies of data, on 2 different media, with 1 copy offsite). A well-defined disaster recovery plan should Artikel steps for restoring systems and data, assigning roles and responsibilities to different personnel, and establishing communication protocols.
A simulated ransomware attack scenario can be included in regular disaster recovery drills to ensure preparedness.
Essential Steps for Post-Ransomware Attack Forensic Analysis
A thorough forensic analysis is crucial for understanding the attack, identifying vulnerabilities, and preventing future incidents. The following steps are essential:
- Secure the compromised network to prevent further data loss or compromise.
- Create a forensic image of the affected systems.
- Analyze the ransomware payload to identify its characteristics and origin.
- Identify the initial infection vector.
- Analyze network logs and system logs to track the attacker’s actions.
- Document all findings and create a comprehensive report.
The Role of Manufacturers and Users
The vulnerability of network-connected wrenches to ransomware highlights a critical shared responsibility between manufacturers and end-users. Both parties play a vital role in securing these increasingly common industrial tools and preventing costly disruptions. A collaborative approach is essential to mitigate the risks associated with these attacks.Manufacturers bear the primary responsibility for building secure devices from the ground up.
This involves implementing robust security protocols during the design phase, incorporating secure boot mechanisms, and regularly updating firmware to patch vulnerabilities. Failure to do so exposes users to significant risks and can severely damage a manufacturer’s reputation.
Manufacturer Responsibilities in Ensuring Security
Manufacturers must prioritize security throughout the entire product lifecycle. This includes conducting thorough security assessments during the design and development phases, implementing secure coding practices, and utilizing secure hardware components. Regular security audits and penetration testing are crucial to identify and address potential vulnerabilities before products reach the market. Furthermore, manufacturers should provide clear and easily accessible documentation for users on how to securely configure and maintain their wrenches, including best practices for firmware updates and network security.
A proactive approach to vulnerability disclosure and patching is essential, with a commitment to timely release of security updates and clear communication with users about known vulnerabilities and their remediation. Finally, manufacturers should invest in robust incident response plans to effectively address security incidents that may occur.
User Responsibilities in Maintaining Security
Users also play a crucial role in maintaining the security of their network-connected wrenches. This begins with carefully selecting vendors with a proven track record of security practices. Users should ensure that their wrenches are kept up-to-date with the latest firmware versions, following the manufacturer’s instructions carefully. Implementing strong network security measures, such as firewalls and intrusion detection systems, is also vital.
Regular security assessments of the industrial network are necessary to identify and address any vulnerabilities. User training on security best practices is essential, and employees should be educated on the potential threats and how to recognize and report suspicious activity. Finally, developing and regularly testing incident response plans is crucial to minimize the impact of a successful ransomware attack.
Collaboration Between Manufacturers and Users
Effective collaboration between manufacturers and users is essential for mitigating ransomware threats. This can involve establishing open communication channels for reporting vulnerabilities and receiving security updates. Manufacturers should actively engage with user communities to gather feedback and address concerns. Joint vulnerability assessments and penetration testing can identify weaknesses and inform the development of effective mitigation strategies. Industry-wide standards and best practices should be developed and adopted to ensure a consistent level of security across the industry.
This collaborative approach fosters a more secure ecosystem for network-connected wrenches.
Approaches to Vulnerability Management
Different approaches to vulnerability management exist, ranging from reactive patching to proactive threat hunting. Reactive patching involves addressing vulnerabilities only after they have been exploited, often resulting in delayed responses and increased risk. Proactive threat hunting, on the other hand, involves actively searching for vulnerabilities before they are exploited, enabling timely remediation. A combination of both approaches, focusing on proactive measures with a reactive plan in place, offers the most comprehensive security posture.
This includes regular security audits, penetration testing, and the implementation of a vulnerability management system to track and prioritize the remediation of identified vulnerabilities. Implementing a strong security information and event management (SIEM) system can help to detect and respond to security incidents more effectively.
Recommendations for Improving Industrial Network Security
To improve the overall security posture of industrial networks that include network-connected wrenches, several recommendations should be considered. These include:
- Implement robust network segmentation to isolate critical systems from less critical ones.
- Utilize strong authentication mechanisms, such as multi-factor authentication, to restrict access to sensitive systems.
- Regularly update firmware and software on all devices connected to the network.
- Implement intrusion detection and prevention systems to monitor network traffic for malicious activity.
- Conduct regular security assessments and penetration testing to identify and address vulnerabilities.
- Develop and regularly test incident response plans to minimize the impact of a successful attack.
- Establish a clear communication protocol for reporting and responding to security incidents.
- Invest in employee training programs to raise awareness of security threats and best practices.
Future Implications and Mitigation Strategies
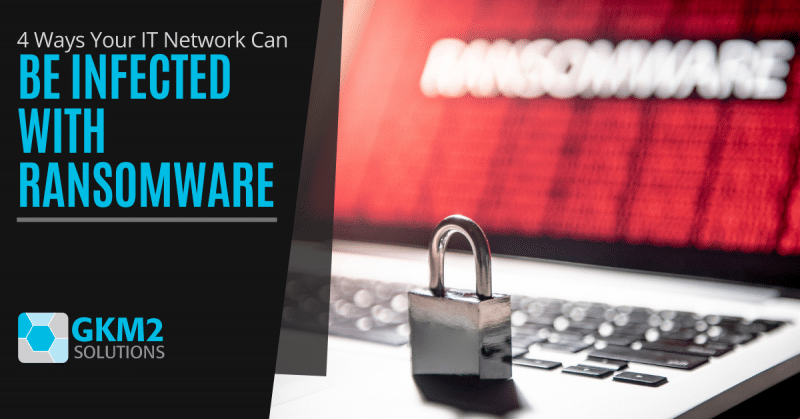
The vulnerability of network-connected wrenches to ransomware presents a significant long-term threat to manufacturing efficiency and global supply chains. The potential for widespread disruption, financial losses, and reputational damage necessitates proactive strategies to mitigate these risks and secure the burgeoning Industrial Internet of Things (IIoT). Failure to address these vulnerabilities could lead to significant economic consequences and a decline in trust in connected industrial equipment.The long-term implications of ransomware attacks targeting network-connected wrenches extend beyond immediate production halts.
Disrupted supply chains, increased insurance premiums, and the potential for regulatory fines represent substantial ongoing costs. Furthermore, the erosion of public trust in the reliability and security of smart manufacturing technologies could hinder adoption and innovation in the sector. A major ransomware attack could cause significant delays in critical projects, impacting everything from automotive production to aerospace manufacturing.
For example, a ransomware attack crippling a major automotive assembly plant could result in thousands of vehicles being delayed, leading to significant financial losses for the manufacturer and impacting supply chains worldwide.
Emerging Technologies and Mitigation Strategies
Several emerging technologies and strategies are crucial for mitigating future ransomware threats against network-connected wrenches. These include robust multi-factor authentication, regular software updates and patching, network segmentation to isolate critical systems, and the implementation of advanced threat detection systems. Utilizing immutable logging systems can also provide a crucial audit trail to help investigate and respond to attacks. Finally, rigorous employee training on cybersecurity best practices is essential to prevent social engineering attacks that could lead to a breach.
The Role of Artificial Intelligence and Machine Learning in Enhancing Wrench Network Security
AI and machine learning offer powerful tools for enhancing wrench network security. AI-powered anomaly detection systems can identify unusual patterns in network traffic or wrench behavior, potentially indicating a ransomware attack in its early stages. Machine learning algorithms can be trained to recognize and classify malicious code, improving the effectiveness of existing security software. Furthermore, AI can assist in automating security tasks such as vulnerability scanning and patch management, reducing the workload on security teams.
Imagine an AI system that continuously monitors the torque readings of a network-connected wrench and identifies deviations from expected patterns – a potential indicator of compromised functionality or a malicious actor manipulating the device.
Areas for Future Research in Securing Industrial IoT Devices
Future research should focus on developing more robust and secure communication protocols for IIoT devices, including network-connected wrenches. This includes exploring the use of blockchain technology for secure data storage and transmission, as well as developing advanced encryption techniques to protect sensitive data. Furthermore, research should focus on developing more effective methods for detecting and responding to zero-day exploits – vulnerabilities that are unknown to security researchers until they are actively exploited.
Another critical area of research is the development of standardized security frameworks for IIoT devices, providing a common set of guidelines and best practices for manufacturers and users.
Visual Representation of a Ransomware Attack Impact
Imagine a flowchart depicting a manufacturing process, perhaps an automotive assembly line. The flowchart shows various stages, each involving network-connected wrenches for precise torque control. A highlighted section of the flowchart, representing the wrench network, shows a red “X” or a padlock icon with a red slash through it, symbolizing the ransomware attack. Downstream from this point, the flowchart branches off into several paths representing various disruptions: production halts (represented by a stop sign), delayed shipments (depicted by a slow-moving truck icon), financial losses (indicated by a downward-trending graph), and potential safety concerns (represented by an exclamation point in a triangle).
The flowchart visually illustrates the cascading effect of a ransomware attack on a seemingly small component, such as a network-connected wrench, leading to widespread disruption across the entire manufacturing process.
Last Recap
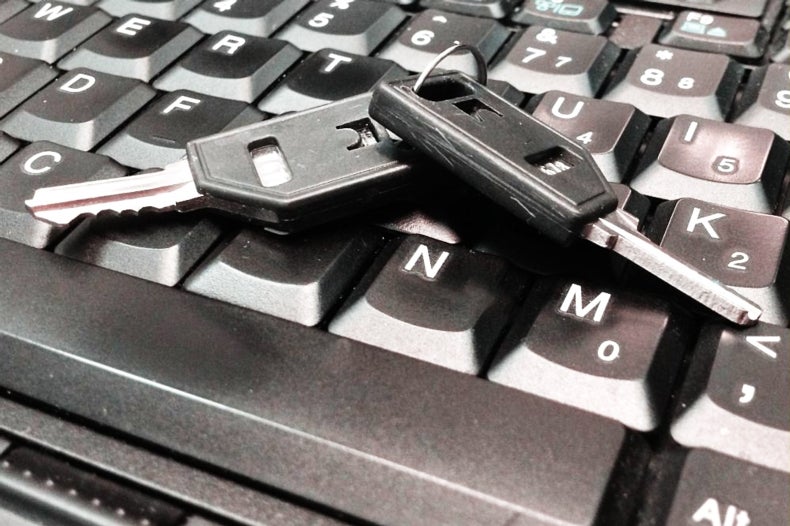
The vulnerability of network-connected wrenches to ransomware attacks highlights a critical need for increased security awareness and proactive measures within the industrial IoT landscape. From robust security protocols and regular firmware updates to comprehensive incident response plans and collaborative efforts between manufacturers and users, a multi-pronged approach is essential. Ignoring this threat isn’t an option; the potential consequences are too significant.
By embracing proactive security practices and staying ahead of emerging threats, we can protect our critical infrastructure and ensure the continued smooth operation of our increasingly connected world.
FAQ Explained: Network Connected Wrenches Are Now Vulnerable To Ransomware Attacks
What types of data are at risk in a ransomware attack on network-connected wrenches?
Data at risk includes operational data (wrench torque settings, usage logs), configuration settings, and potentially sensitive intellectual property related to manufacturing processes.
Can air-gapped wrenches be affected by ransomware?
No, air-gapped wrenches, those not connected to a network, are not directly vulnerable to ransomware attacks. However, the overall network’s security posture remains important to prevent lateral movement of the attack.
What is the role of insurance in mitigating ransomware risks for network-connected wrenches?
Cyber insurance can help cover some of the financial losses associated with a ransomware attack, including ransom payments (though this is controversial), data recovery costs, and business interruption expenses. However, it’s crucial to have robust security measures in place as well.
How can I determine if my network-connected wrenches are vulnerable?
Regular vulnerability scans and penetration testing can identify weaknesses in your network and devices. Checking for and installing available firmware updates is also vital.