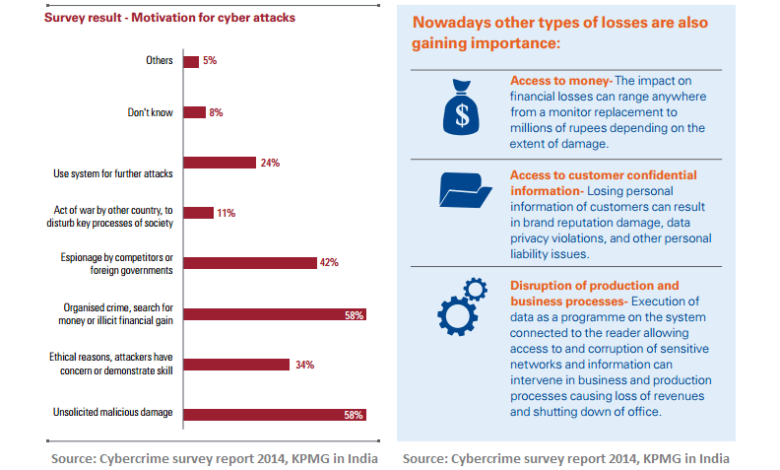
Study Confirms Manufacturings Cyber Vulnerability
Study confirms manufacturing companies are more vulnerable to cyber attacks, a fact that’s chillingly true in today’s interconnected world. Manufacturing facilities, with their intricate networks of industrial control systems (ICS) and operational technology (OT), represent a juicy target for malicious actors. From crippling ransomware attacks to sophisticated data breaches, the consequences can be devastating, impacting not just the bottom line but also national security and public safety.
This vulnerability isn’t just about outdated technology; it’s also about human error and a lack of robust cybersecurity strategies. We’ll delve into the specifics of these vulnerabilities, exploring real-world examples and offering practical solutions to strengthen defenses.
The sheer complexity of modern manufacturing plants, with their blend of legacy systems and cutting-edge automation, creates a unique cybersecurity challenge. The interconnected nature of these systems means a single point of failure can cascade into widespread disruption. We’ll examine the various entry points for cyberattacks, from phishing emails targeting employees to sophisticated exploits targeting vulnerabilities in ICS/OT.
We’ll also discuss the critical role of human error and the need for comprehensive employee training programs. Ultimately, this exploration aims to provide a clearer understanding of the threats facing manufacturers and the steps they can take to mitigate their risk.
Vulnerability Vectors in Manufacturing
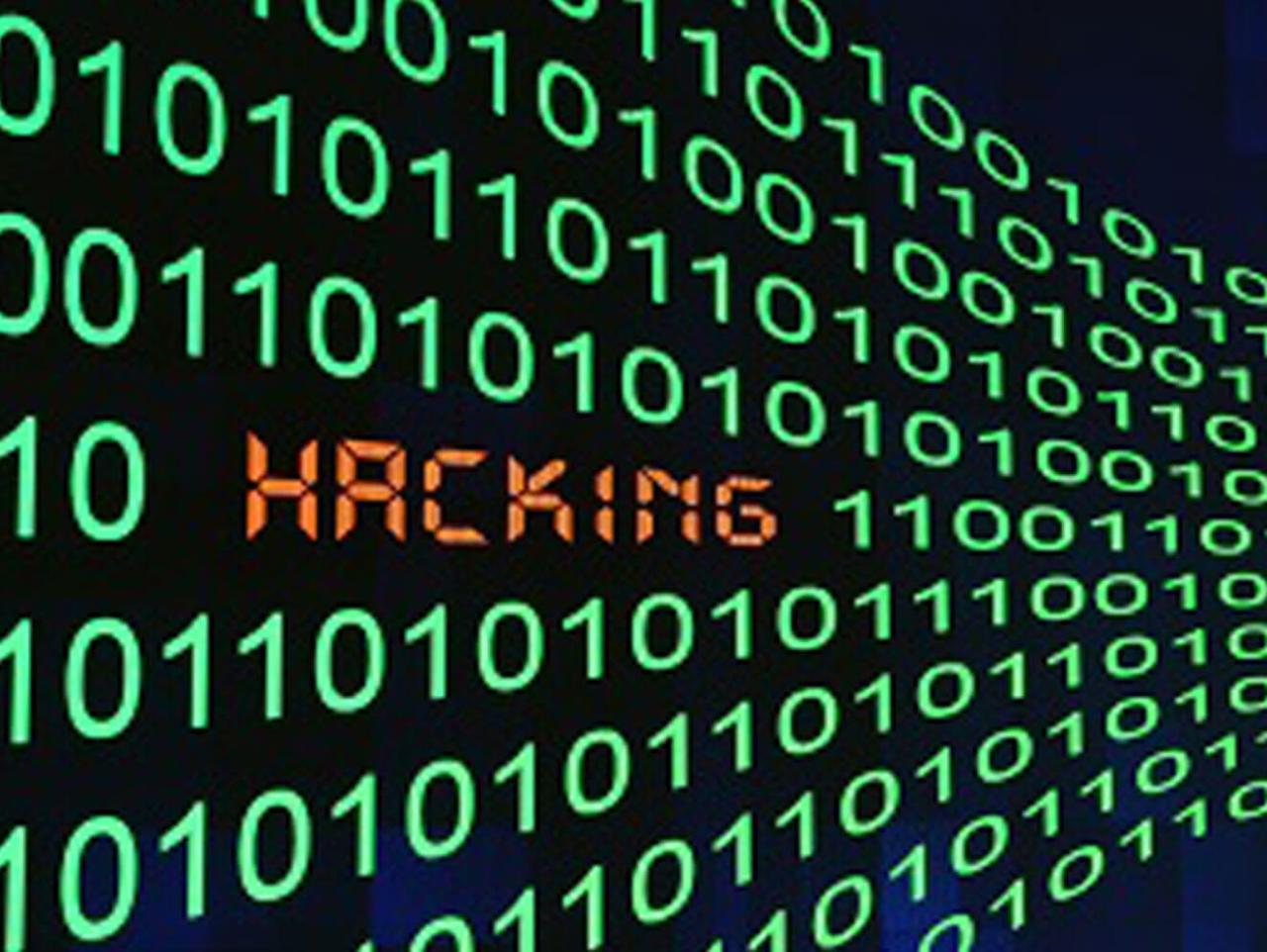
The recent study confirming the heightened vulnerability of manufacturing companies to cyberattacks underscores the critical need to understand the various entry points exploited by malicious actors. These attacks aren’t just about data breaches; they can cripple production lines, disrupt supply chains, and even endanger human lives. Understanding these vulnerabilities is the first step towards effective mitigation.Manufacturing environments present a unique landscape of cybersecurity challenges, differing significantly from traditional office settings.
The convergence of Information Technology (IT) and Operational Technology (OT) systems, often with aging infrastructure and a lack of robust security practices, creates a fertile ground for attackers.
Common Entry Points for Cyberattacks
The following table summarizes common vulnerability types, their descriptions, examples, and potential mitigation strategies. It’s important to remember that these are not mutually exclusive; multiple vulnerabilities can often be exploited in a single attack.
Vulnerability Type | Description | Example | Mitigation Strategy |
---|---|---|---|
Phishing and Social Engineering | Tricking employees into revealing sensitive information or granting access to systems. | An email appearing to be from a supplier requesting login credentials. | Security awareness training, multi-factor authentication (MFA), email filtering. |
Remote Access Vulnerabilities | Exploiting weaknesses in remote access tools and protocols to gain unauthorized access to systems. | Unpatched VPN server allowing unauthorized access to the plant network. | Regular patching, strong password policies, access control lists (ACLs), VPN segmentation. |
Software Vulnerabilities | Exploiting known vulnerabilities in software applications and operating systems. | Unpatched SCADA software with known exploits. | Regular patching and updates, vulnerability scanning, software asset management. |
Hardware Vulnerabilities | Exploiting weaknesses in physical hardware devices. | Compromised Programmable Logic Controller (PLC) with a backdoor. | Secure hardware procurement, physical access controls, regular hardware audits. |
Vulnerabilities of Industrial Control Systems (ICS) and Operational Technology (OT)
ICS and OT environments, the heart of manufacturing operations, are often characterized by legacy systems, limited visibility, and a lack of robust security protocols. These systems, responsible for controlling physical processes, are frequently vulnerable to attacks that can directly impact production. For example, a compromised PLC could cause a malfunction in a critical process, leading to production downtime, damage to equipment, or even safety hazards.
The lack of segmentation between IT and OT networks further exacerbates this risk, allowing attackers to easily move laterally from one system to another. The reliance on proprietary protocols and specialized hardware also makes securing these environments particularly challenging.
Cybersecurity Vulnerabilities of Legacy Systems vs. Modern Equipment
Legacy systems, often found in older manufacturing plants, present significantly higher cybersecurity risks compared to modern, connected equipment. These older systems often lack the built-in security features of newer systems, making them easier targets for attackers. Furthermore, obtaining security patches and updates for legacy systems can be difficult or impossible, leaving them perpetually vulnerable. In contrast, modern, connected equipment often incorporates advanced security features such as encryption, intrusion detection systems, and remote diagnostics.
However, the increased connectivity of these systems also presents new challenges, as they can create new attack vectors if not properly secured. The contrast is stark: legacy systems are vulnerable due to age and lack of updates, while modern systems can be vulnerable due to their increased connectivity and reliance on network infrastructure. A balanced approach, integrating modern security practices with careful management of legacy systems, is crucial.
Impact of Cyberattacks on Manufacturing Operations
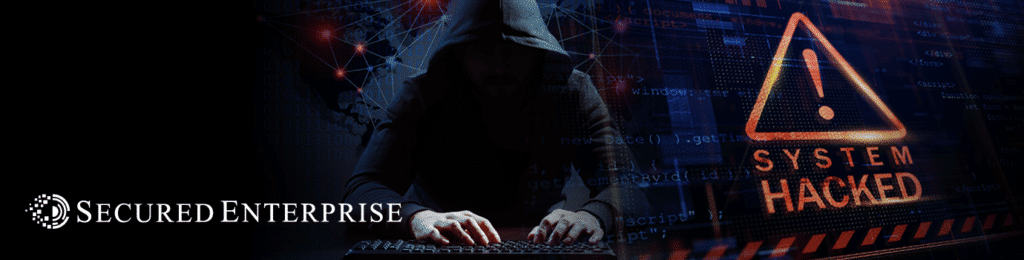
The increasing interconnectedness of manufacturing systems, coupled with the reliance on legacy systems and a sometimes-lacking cybersecurity culture, makes the sector a prime target for cybercriminals. The consequences of successful attacks can be devastating, impacting not only the bottom line but also the safety and security of workers and the broader supply chain. This section will explore the real-world effects of cyberattacks on manufacturing operations.The financial ramifications of cyberattacks on manufacturing companies are substantial and far-reaching.
Beyond the immediate costs of remediation and recovery, significant losses stem from prolonged downtime, data breaches, and the erosion of hard-earned reputation. The ripple effects extend throughout the supply chain, impacting numerous businesses and consumers alike.
Examples of Real-World Cyberattacks and Their Consequences
The following examples highlight the severity and variety of cyber threats facing the manufacturing sector. These attacks demonstrate the potential for significant disruption and financial losses.
- NotPetya (2017): This devastating ransomware attack, initially targeting Ukrainian accounting software, spread globally, significantly impacting manufacturing companies. Many firms experienced extensive production downtime, data loss, and substantial financial losses due to disrupted operations and the costs of recovery. The widespread nature of the attack highlighted the interconnectedness of global supply chains and the cascading effects of a single incident.
Estimates of the global economic impact of NotPetya range into the billions of dollars.
- Target (2013): While not strictly a manufacturing company, Target’s data breach, which compromised millions of customer credit card numbers, underscored the vulnerability of supply chain partners. Many manufacturing companies rely on third-party vendors for various services, and a breach at one point in the chain can have cascading effects on others, including damage to reputation and potential legal liabilities.
- Stuxnet (2010): This sophisticated worm, widely believed to be state-sponsored, targeted Iranian nuclear facilities. While not directly impacting a manufacturing company in the traditional sense, Stuxnet demonstrated the potential for highly targeted attacks to cripple critical infrastructure and industrial control systems, highlighting the vulnerability of sophisticated machinery to malicious code. The attack demonstrated the potential for significant physical damage beyond mere data loss.
Financial Losses from Cyberattacks
Production downtime represents a major financial blow to manufacturers. Lost production translates directly into lost revenue, and the costs of bringing systems back online can be substantial. This includes the cost of IT specialists, recovery of data, and potential regulatory fines. Data breaches, resulting in the theft of intellectual property, customer data, or sensitive business information, lead to further financial losses through legal fees, remediation costs, and potential reputational damage.
Reputational damage can be especially costly, leading to decreased customer trust and reduced market share. These losses are difficult to quantify precisely, but the cumulative effect can be crippling for even large companies.
Supply Chain Disruption from Cyberattacks
Manufacturing relies heavily on complex and interconnected supply chains. A successful cyberattack against a single link in this chain can create widespread disruption. For example, a compromised supplier might be unable to deliver essential components, leading to production delays or even complete shutdowns. This disruption can ripple through the entire supply chain, impacting multiple companies and causing significant financial losses and reputational damage across the board.
The cascading effect of these disruptions can be severe and prolonged, making supply chain resilience a critical aspect of cybersecurity for manufacturing companies.
The Role of Human Error in Manufacturing Cyberattacks
Human error remains a significant vulnerability in the cybersecurity landscape of manufacturing companies. Despite sophisticated technological safeguards, the weakest link often lies in the human element. A lack of awareness, inadequate training, and susceptibility to social engineering tactics leave manufacturers open to a wide range of cyber threats, often resulting in significant financial losses and operational disruptions. Understanding these vulnerabilities is crucial for developing effective mitigation strategies.
Many common human errors contribute to successful cyberattacks within manufacturing settings. These errors often stem from a combination of insufficient training, rushed work environments, and a lack of understanding about the potential consequences of seemingly innocuous actions. For instance, clicking on a malicious link in a phishing email, reusing passwords across multiple platforms, or failing to report suspicious activity can all provide entry points for cybercriminals.
Common Human Errors Contributing to Manufacturing Cyberattacks
Several recurring human errors significantly increase the risk of successful cyberattacks. These errors are often preventable through targeted training and robust security protocols.
- Falling prey to phishing scams: Employees may unknowingly open malicious emails containing infected attachments or links, granting attackers access to company systems.
- Weak or reused passwords: Using easily guessable passwords or reusing the same password across multiple accounts creates a significant vulnerability. If one account is compromised, the attacker gains access to others.
- Ignoring security updates and patches: Failure to install critical software updates leaves systems vulnerable to known exploits, providing attackers with easy access points.
- Improper disposal of sensitive data: Failing to securely dispose of hard drives, documents, or other physical media containing sensitive information can lead to data breaches.
- Unsecured mobile devices: Using personal or unsecured mobile devices to access company networks or data increases the risk of malware infection and data breaches.
- Lack of reporting suspicious activity: Employees may fail to report suspicious emails, websites, or unusual system behavior, allowing attackers to remain undetected for extended periods.
Social Engineering Tactics Exploited in Manufacturing Environments
Social engineering techniques are frequently used to manipulate employees into divulging sensitive information or granting access to systems. These tactics exploit human psychology and trust to bypass technical security measures.
- Phishing emails impersonating executives or vendors: Attackers create convincing emails that appear to come from trusted sources, requesting sensitive information or access credentials.
- Pretexting: Attackers create a false scenario to trick employees into providing information or taking actions that compromise security. For example, an attacker might pose as a technician needing access to a system to “troubleshoot a problem.”
- Baiting: Attackers offer enticing rewards or incentives (e.g., a free gift card) to lure employees into clicking on malicious links or downloading infected files.
- Quid pro quo: Attackers offer a service or assistance in exchange for sensitive information. For instance, they might offer to help with a technical issue, but only after gaining access to the employee’s credentials.
A Cybersecurity Awareness Training Program for Manufacturing Employees
A comprehensive training program is crucial for mitigating the risks associated with human error. This program should be tailored to the specific needs and roles of employees within the manufacturing environment.
The program should include modules covering:
- Identifying and reporting phishing attempts: Training on recognizing the hallmarks of phishing emails, such as suspicious links, grammatical errors, and urgent requests for information.
- Password security best practices: Educating employees on creating strong, unique passwords and utilizing password managers.
- Safe handling of sensitive data: Training on proper procedures for storing, transmitting, and disposing of sensitive information.
- Recognizing and reporting suspicious activity: Educating employees on what constitutes suspicious activity and establishing clear reporting procedures.
- Security awareness best practices for mobile devices: Training on securing mobile devices used to access company networks and data.
- Regular refresher training and simulated phishing exercises: Reinforcing learned behaviors and testing employee knowledge through regular training and simulated attacks.
Strengthening Cybersecurity Defenses in Manufacturing
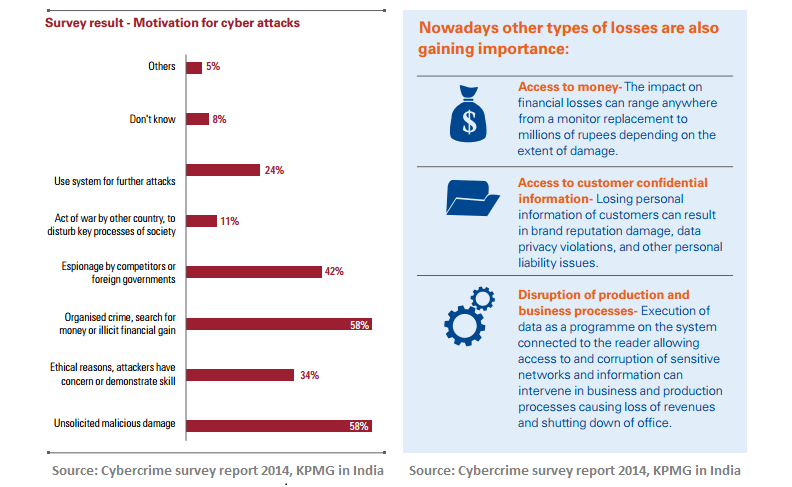
The vulnerability of manufacturing companies to cyberattacks is undeniable. However, proactive implementation of robust security protocols can significantly mitigate this risk, protecting critical infrastructure, intellectual property, and ultimately, the bottom line. Investing in cybersecurity is not just a cost; it’s a strategic imperative for survival in today’s digital landscape. This section Artikels key strategies and prioritized investments for strengthening cybersecurity defenses within the manufacturing sector.
Implementing comprehensive cybersecurity measures requires a multi-layered approach, addressing vulnerabilities at every stage of the manufacturing process. This includes securing industrial control systems (ICS), implementing robust access controls, and establishing a culture of cybersecurity awareness throughout the organization. Regular security assessments, incident response planning, and employee training are all critical components of a strong defense. The effectiveness of these measures hinges on a combination of technological solutions and well-defined processes.
Best Practices for Securing Industrial Control Systems and Operational Technology
Industrial Control Systems (ICS) and Operational Technology (OT) environments present unique challenges to cybersecurity. Their age, often legacy systems, and integration with physical processes make them particularly vulnerable. Therefore, a specialized approach to security is necessary.
- Network Segmentation: Isolating ICS networks from the corporate network limits the impact of a breach. This can be achieved through firewalls, VLANs, and other network segmentation techniques.
- Regular Patching and Updates: Outdated software and firmware are prime targets for attackers. Implementing a robust patching and update schedule is crucial for mitigating known vulnerabilities. This requires careful planning to avoid disrupting operations.
- Intrusion Detection and Prevention Systems (IDPS): These systems monitor network traffic for malicious activity and can automatically block or alert on suspicious events. Specialized IDPS solutions are available for ICS environments.
- Access Control: Strict access control measures, including strong passwords, multi-factor authentication (MFA), and role-based access control (RBAC), are essential to limit unauthorized access to critical systems. Principle of least privilege should be strictly enforced.
- Data Backup and Recovery: Regular backups of critical data and systems are essential to ensure business continuity in the event of a cyberattack. A well-defined disaster recovery plan is also crucial.
Prioritized Cybersecurity Investments for Manufacturing Companies
Budget constraints are a reality for many manufacturing companies. Prioritizing cybersecurity investments is crucial to maximize impact and minimize financial burden. A phased approach, focusing on the most critical vulnerabilities first, is often the most effective strategy.
- Network Segmentation and Access Control: These foundational measures provide the most significant return on investment by limiting the impact of a successful breach. Implementing strong firewalls and robust authentication mechanisms should be the first priority.
- Employee Security Awareness Training: Human error is a major factor in many cyberattacks. Investing in comprehensive security awareness training for all employees is crucial to reduce the risk of phishing attacks and other social engineering techniques. Regular training and phishing simulations are key.
- Intrusion Detection and Prevention Systems (IDPS): Once basic network security is in place, deploying IDPS solutions provides real-time monitoring and protection against advanced threats. This can be implemented incrementally, focusing on the most critical systems first.
- Vulnerability Scanning and Penetration Testing: Regular vulnerability assessments and penetration testing help identify and address security weaknesses before attackers can exploit them. This should be a recurring investment, ideally conducted annually or semi-annually.
- Incident Response Planning: Having a well-defined incident response plan in place is crucial for minimizing the impact of a successful attack. This involves establishing clear procedures for identifying, containing, and recovering from security incidents. This plan should be regularly tested and updated.
Regulatory Compliance and Cybersecurity in Manufacturing
The manufacturing sector faces increasing pressure to bolster its cybersecurity posture, driven not only by the rising threat landscape but also by a tightening regulatory environment. Failure to comply with relevant regulations can lead to significant financial penalties, reputational damage, and even operational disruptions. Understanding and adhering to these standards is crucial for maintaining business continuity and protecting sensitive data.The implications of non-compliance extend far beyond simple fines.
Data breaches resulting from inadequate cybersecurity can expose confidential customer information, intellectual property, and trade secrets, leading to legal battles, loss of market share, and damage to brand trust. In some sectors, non-compliance can also result in operational shutdowns, impacting production schedules and potentially jeopardizing supply chains. Proactive compliance, therefore, is not merely a legal requirement but a strategic imperative for long-term success.
Relevant Industry Regulations and Standards
Several regulations and standards directly impact cybersecurity in manufacturing. These vary depending on the specific industry, geographical location, and the type of data handled. Key examples include the NIST Cybersecurity Framework (CSF), which provides a voluntary framework for improving cybersecurity practices, and the ISO 27001 standard, which Artikels a comprehensive information security management system (ISMS). Industry-specific regulations, such as those governing the automotive, medical device, or aerospace sectors, often impose even more stringent requirements.
Compliance with these regulations often involves implementing specific security controls, conducting regular audits, and demonstrating ongoing compliance to regulatory bodies. Failure to meet these requirements can result in substantial penalties and legal repercussions.
Penalties for Non-Compliance
Non-compliance with cybersecurity regulations can result in a wide range of penalties. These can include significant financial fines, legal action from affected parties, and reputational damage. For example, the General Data Protection Regulation (GDPR) in Europe levies substantial fines for organizations that fail to protect personal data adequately. In the United States, various state-level regulations and industry-specific laws also impose penalties for cybersecurity breaches and non-compliance.
Beyond financial penalties, the loss of customer trust and damage to brand reputation can have long-term negative impacts on a company’s profitability and sustainability. These reputational risks can be as damaging, if not more so, than the direct financial penalties.
Conducting Regular Security Audits and Penetration Testing
Regular security audits and penetration testing are essential components of a robust cybersecurity program. Security audits involve a systematic review of an organization’s security controls and practices to identify vulnerabilities and weaknesses. These audits assess compliance with relevant regulations and standards, and provide recommendations for improvement. Penetration testing, on the other hand, simulates real-world cyberattacks to identify exploitable vulnerabilities in systems and networks.
These tests can uncover weaknesses that might be missed by traditional security audits. Both security audits and penetration testing should be conducted regularly, with the frequency determined by the organization’s risk profile and the sensitivity of the data it handles. The results of these assessments should be used to inform ongoing improvements to the organization’s cybersecurity defenses.
A recent study confirms manufacturing companies are prime targets for cyberattacks, highlighting their often outdated security systems. Strengthening defenses is crucial, and that’s where modern development approaches like those discussed in this article on domino app dev, the low-code and pro-code future , become incredibly important. These methods can help manufacturers build more secure and agile applications, reducing their vulnerability to sophisticated attacks.
A well-defined process for remediation of identified vulnerabilities is crucial for ensuring the effectiveness of these activities. This process should include clear timelines, responsible parties, and regular reporting on progress.
The Future of Cybersecurity in Manufacturing
The manufacturing landscape is undergoing a rapid digital transformation, driven by Industry 4.0 initiatives and the increasing adoption of interconnected systems. This interconnectedness, while offering significant benefits in terms of efficiency and productivity, significantly expands the attack surface for cybercriminals. The future of cybersecurity in manufacturing hinges on proactively addressing these evolving threats and embracing innovative technologies to build resilient and secure operations.
Emerging Cybersecurity Threats in Manufacturing
The threat landscape for manufacturing is constantly evolving, with new attack vectors emerging regularly. Advanced Persistent Threats (APTs), often state-sponsored, are becoming more sophisticated, targeting intellectual property, sensitive data, and critical infrastructure. Ransomware attacks continue to pose a significant risk, potentially disrupting production lines and causing substantial financial losses. Furthermore, the increasing reliance on cloud-based services and the Internet of Things (IoT) devices introduces vulnerabilities that need careful management.
The exploitation of vulnerabilities in legacy systems, often lacking robust security features, remains a significant concern. Finally, supply chain attacks, targeting vulnerabilities in the manufacturing ecosystem’s various components, are growing in frequency and impact. For example, a compromised supplier’s software could provide a backdoor into the entire manufacturing network.
Innovative Cybersecurity Technologies and Applications in Manufacturing
Several innovative cybersecurity technologies offer promising solutions to address the growing threats facing the manufacturing sector. Artificial intelligence (AI) and machine learning (ML) are being used to detect anomalies and predict potential attacks by analyzing vast amounts of data from various sources. This proactive approach can significantly reduce response times and minimize the impact of successful breaches. Blockchain technology can enhance supply chain security by providing a transparent and tamper-proof record of materials and components throughout the manufacturing process.
This helps prevent the introduction of malicious components or counterfeit parts. Zero Trust security models, which assume no implicit trust, are gaining traction. These models verify every user and device before granting access to resources, regardless of location. This significantly reduces the impact of compromised credentials. Advanced threat detection and response systems, incorporating threat intelligence and automated incident response capabilities, are critical for rapid containment and remediation of cyberattacks.
For instance, a system that automatically isolates a compromised machine upon detection can limit the spread of malware.
Evolution of Cybersecurity Threats and Defenses in Manufacturing (2013-2023), Study confirms manufacturing companies are more vulnerable to cyber attacks
Imagine a graph charting the evolution of cybersecurity in manufacturing over the past decade. The X-axis represents time (2013-2023), and the Y-axis represents the sophistication of both threats and defenses. From 2013 to roughly 2017, the threat curve shows a steady increase, reflecting the growing prevalence of relatively simple attacks like phishing and malware. Defense mechanisms during this period primarily focused on perimeter security and basic antivirus solutions.
Around 2017, the threat curve sharply accelerates upward, reflecting the rise of more sophisticated attacks such as APTs and ransomware. The defense curve, while also rising, lags behind, showing a need to catch up with evolving threats. From 2020 onwards, both curves continue to rise, but the defense curve demonstrates a steeper incline, indicating a growing adoption of advanced technologies like AI, ML, and zero-trust architectures.
The gap between the threat and defense curves is still present, highlighting the ongoing arms race between attackers and defenders in the manufacturing sector. The ideal scenario would be for the defense curve to consistently surpass the threat curve, ensuring a proactive and robust security posture.
Final Thoughts
The vulnerability of manufacturing companies to cyberattacks is a serious and growing concern. While the challenges are significant, the good news is that proactive measures can significantly reduce risk. By understanding the common attack vectors, investing in robust security protocols, and prioritizing employee training, manufacturers can bolster their defenses and protect their operations, supply chains, and reputations. The future of manufacturing cybersecurity hinges on a collaborative effort, encompassing technological innovation, regulatory compliance, and a fundamental shift in organizational culture towards a proactive, security-first mindset.
Ignoring this threat is simply not an option.
Top FAQs: Study Confirms Manufacturing Companies Are More Vulnerable To Cyber Attacks
What are the most common types of ransomware used against manufacturing companies?
While various ransomware strains are used, those known for their ability to encrypt critical ICS/OT systems and cause significant operational disruption are most prevalent. Specific strains change frequently, so staying updated on threat intelligence is crucial.
How much does a cybersecurity breach cost a manufacturing company, on average?
The cost varies drastically depending on the size of the company, the extent of the breach, and the resulting downtime. However, estimates range from hundreds of thousands to millions of dollars, encompassing direct costs like remediation and indirect costs like lost revenue and reputational damage.
Are there government incentives for manufacturers to improve cybersecurity?
Many governments offer grants, tax breaks, or other incentives to encourage businesses, including manufacturers, to improve their cybersecurity posture. Check with your local or national government agencies for details on available programs.