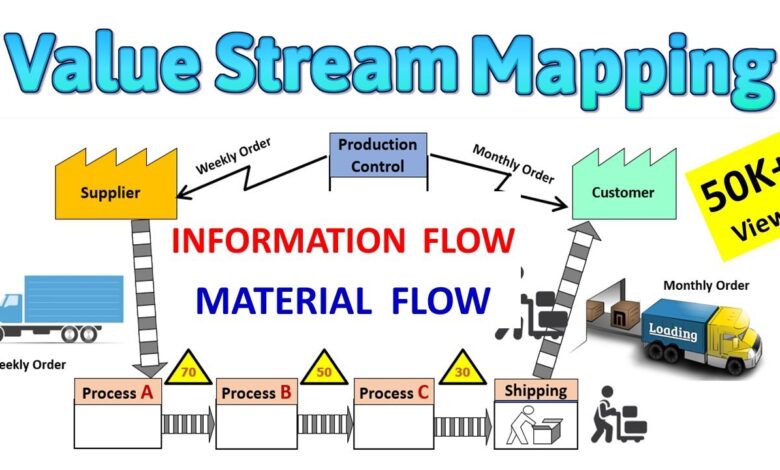
What is a Value Stream Manager?
What is a value stream manager? It’s a question that’s increasingly relevant in today’s fast-paced business world. Essentially, a value stream manager is a process improvement specialist focused on optimizing the flow of value from start to finish for a product or service. They’re not just about fixing problems; they’re about proactively identifying and eliminating waste at every stage, ensuring efficiency and customer satisfaction.
Think of them as the conductors of a well-oiled machine, orchestrating the entire process to deliver maximum value.
This role requires a unique blend of analytical skills, leadership qualities, and a deep understanding of Lean principles and other process improvement methodologies. They work across departments, collaborating with teams to map out the entire value stream, identify bottlenecks, and implement improvements. It’s a challenging but incredibly rewarding career path for those who enjoy problem-solving and driving positive change within an organization.
Defining the Value Stream Manager Role
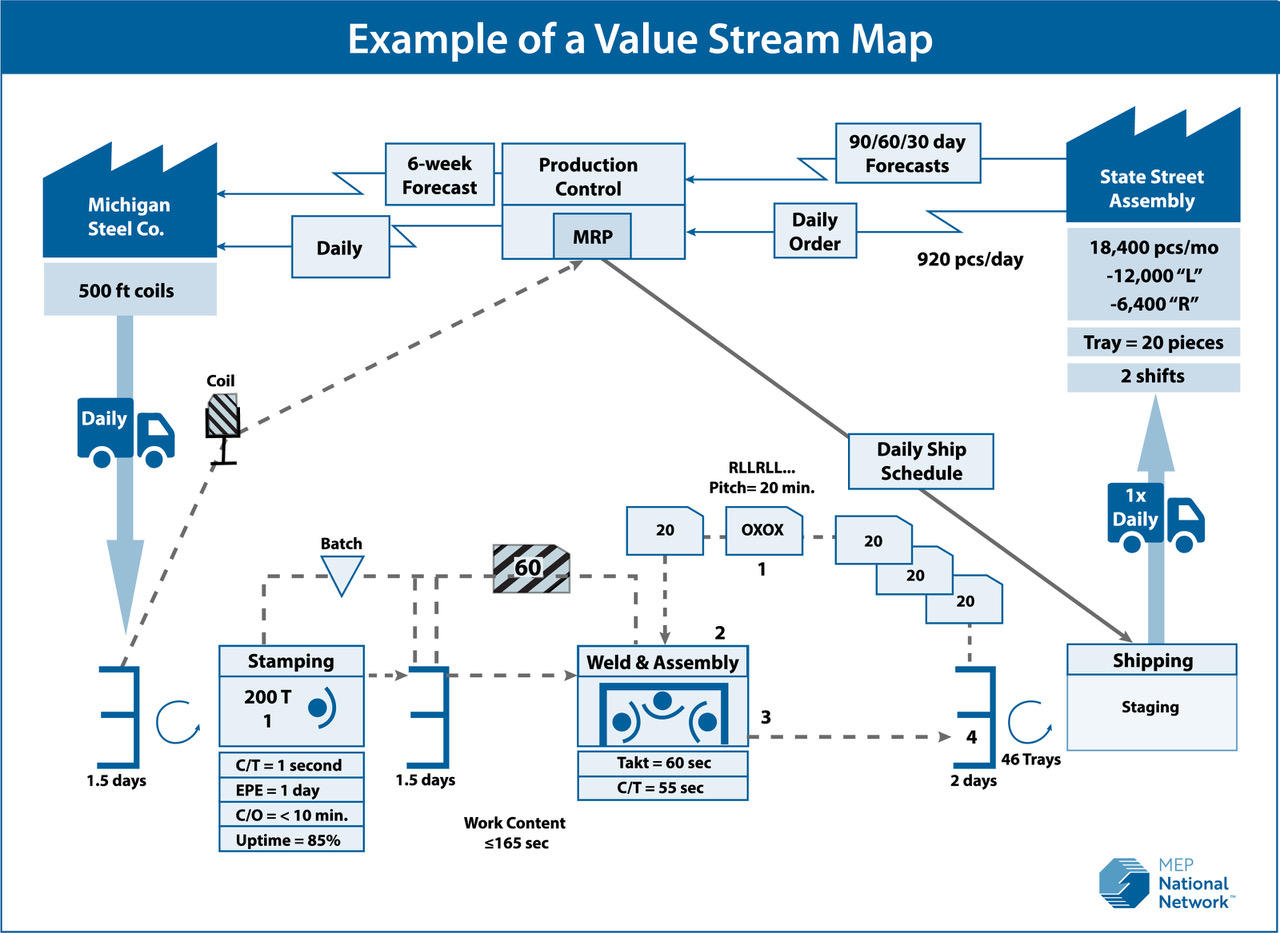
The Value Stream Manager (VSM) is a critical role in today’s lean and agile organizations. They’re the orchestrators of efficiency, tasked with identifying and eliminating waste throughout the entire process of delivering value to the customer. This goes beyond simply managing individual projects; it’s about understanding the big picture and driving continuous improvement across the entire value stream.Core Responsibilities of a Value Stream Manager encompass identifying bottlenecks, analyzing workflow inefficiencies, and implementing process improvements to optimize the flow of work and resources.
They work closely with cross-functional teams, acting as a facilitator and change agent to ensure everyone is aligned and working towards the same goals. This often involves data analysis, process mapping, and the implementation of lean principles such as Kaizen and Kanban. Beyond these immediate tasks, a VSM plays a vital role in fostering a culture of continuous improvement within the organization.
Key Skills and Attributes of Successful Value Stream Managers
Effective Value Stream Managers possess a unique blend of technical and soft skills. Technically, they need a strong understanding of lean methodologies, process improvement techniques, and data analysis. They must be proficient in using various tools for process mapping, data visualization, and performance monitoring. Beyond the technical expertise, strong leadership, communication, and collaboration skills are paramount. They need to be able to influence and motivate cross-functional teams, navigate organizational politics, and build consensus around improvement initiatives.
Problem-solving skills, coupled with a proactive and results-oriented mindset, are also crucial for success in this demanding role. A VSM needs to be comfortable working with ambiguity, adapting to changing priorities, and making data-driven decisions.
Comparison with Similar Roles
While the Value Stream Manager role shares similarities with Project Managers and Process Improvement Managers, there are key distinctions. Project Managers typically focus on delivering specific projects within defined timelines and budgets. Process Improvement Managers concentrate on optimizing individual processes, often within a single department. The VSM, however, takes a broader, more holistic view, focusing on the entire value stream from beginning to end, transcending departmental boundaries.
They are less concerned with the micro-management of individual tasks and more focused on the macro-level optimization of the entire flow of value creation. Think of a project manager as focusing on a single tree, a process improvement manager on a small forest, while the VSM oversees the entire landscape.
Industries Where Value Stream Managers Are Crucial
The Value Stream Management approach is applicable across a wide range of industries. In manufacturing, VSMs are essential for streamlining production processes, reducing lead times, and improving quality. In healthcare, they can optimize patient flow, reduce wait times, and improve overall efficiency. In software development, VSMs play a key role in implementing agile methodologies, accelerating delivery cycles, and improving software quality.
Financial services, logistics, and even the public sector are all benefiting from the implementation of VSM principles, leveraging the expertise of skilled Value Stream Managers to improve efficiency and customer satisfaction. For example, a large bank might employ a VSM to optimize the loan application process, while a logistics company might use one to streamline their supply chain.
Value Stream Mapping and Analysis
Value stream mapping is a powerful tool for a Value Stream Manager, providing a visual representation of all the steps involved in delivering a product or service to a customer. By understanding the flow, bottlenecks, and waste within the process, significant improvements can be made to efficiency and customer satisfaction. This process is iterative, allowing for continuous refinement and optimization.
Creating a Value Stream Map: A Step-by-Step Process
Creating a value stream map involves a systematic approach, moving from a high-level overview to a detailed analysis. The process is collaborative, engaging individuals from across the value stream. This ensures a comprehensive and accurate representation of the current state.
- Define the Scope: Clearly define the product or service and the boundaries of the value stream. This includes specifying the starting point (e.g., order placement) and the ending point (e.g., delivery to the customer).
- Gather Data: Collect data on the process steps, lead times, inventory levels, and any other relevant metrics. This often involves interviews, observations, and reviewing existing documentation.
- Draw the Current State Map: Illustrate the current state of the value stream using standardized symbols. This visual representation should include all steps, material and information flows, inventory levels, and lead times.
- Identify Waste and Bottlenecks: Analyze the current state map to pinpoint areas of waste (e.g., excess inventory, waiting time, unnecessary movement) and bottlenecks (e.g., process steps with long lead times). This is a crucial step for prioritizing improvement opportunities.
- Develop a Future State Map: Based on the identified waste and bottlenecks, design a future state map illustrating how the process could be improved. This involves brainstorming and implementing solutions to eliminate waste and improve efficiency.
- Implement Changes: Implement the proposed changes in a phased approach, monitoring the results and making adjustments as needed.
- Monitor and Review: Continuously monitor the performance of the improved process and review the value stream map periodically to identify further improvement opportunities.
Identifying Waste and Bottlenecks in a Value Stream
Effective identification of waste and bottlenecks requires a systematic approach and a deep understanding of the process. Using a combination of data analysis and visual tools, like the value stream map itself, provides a holistic perspective.Best practices include:
- Walk the Process: Physically walk through the entire value stream to observe the process firsthand. This provides valuable insights that may not be captured through data alone.
- Data Analysis: Analyze process data to identify areas with long lead times, high inventory levels, or frequent defects. This quantitative data supports the qualitative observations from walking the process.
- Gemba Walks: Regular visits to the actual work location (Gemba) allows for observation of the process in real-time, leading to identification of hidden issues and waste.
- Collaboration: Involve team members from across the value stream in the identification process. Their insights and experience are invaluable in identifying potential areas for improvement.
Types of Waste Addressed by a Value Stream Manager
A Value Stream Manager tackles various types of waste, often categorized using the acronym “TIMWOOD”: Transportation, Inventory, Motion, Waiting, Overproduction, Over-processing, Defects. Understanding these waste categories is essential for effective value stream improvement.
Waste Type | Description | Impact on Value Stream | Mitigation Strategy |
---|---|---|---|
Transportation | Unnecessary movement of materials or information. | Increased lead times, higher costs, potential for damage. | Optimize layout, use automation, implement Kanban systems. |
Inventory | Excess materials or work-in-progress (WIP) exceeding immediate needs. | Increased storage costs, risk of obsolescence, hides process problems. | Implement lean inventory management techniques (e.g., Kanban), reduce batch sizes. |
Motion | Unnecessary movement of people or equipment. | Wasted time, increased risk of errors, reduced efficiency. | Improve workplace layout, use ergonomic tools, implement 5S methodology. |
Waiting | Delays in the process due to idle time or bottlenecks. | Increased lead times, reduced throughput, increased costs. | Balance workflow, eliminate bottlenecks, improve communication. |
Overproduction | Producing more than is needed or demanded. | Increased inventory costs, wasted resources, potential for obsolescence. | Implement pull systems (e.g., Kanban), level production. |
Over-processing | Performing more work than is necessary to meet customer requirements. | Increased costs, longer lead times, reduced efficiency. | Simplify processes, eliminate unnecessary steps, use automation. |
Defects | Errors or imperfections in the product or service. | Increased rework costs, customer dissatisfaction, potential for safety issues. | Implement quality control measures, use error-proofing techniques, train employees. |
Implementing Value Stream Improvements
Successfully implementing value stream improvements requires a strategic approach that combines proven methodologies with careful monitoring and adaptation. This involves selecting the right tools, identifying key performance indicators, prioritizing initiatives, and learning from successes and failures along the way. The ultimate goal is to streamline processes, eliminate waste, and deliver superior value to the customer.
Value Stream Improvement Methodologies
Lean and Six Sigma are two prominent methodologies frequently employed for value stream improvement. Lean focuses on eliminating waste (muda) in all forms – overproduction, waiting, transportation, over-processing, inventory, motion, and defects – to optimize processes and maximize value. Six Sigma, on the other hand, uses statistical methods to identify and reduce variation in processes, aiming for near-perfection (six standard deviations from the mean) in quality and efficiency.
Often, a blended approach leveraging the strengths of both methodologies proves most effective. For instance, a company might use Lean principles to map the value stream and identify waste, then apply Six Sigma tools to analyze the root causes of variation in a specific process and implement precise solutions.
Key Performance Indicators (KPIs) for Value Stream Effectiveness
Monitoring progress and demonstrating the impact of value stream improvements requires the use of relevant KPIs. These metrics provide a quantifiable measure of success and guide further optimization efforts.
- Lead Time: The total time it takes to complete a process from start to finish. A shorter lead time indicates improved efficiency.
- Cycle Time: The time it takes to complete a single unit of work. Reducing cycle time enhances productivity.
- Throughput: The rate at which a process completes units of work. Increased throughput reflects improved capacity.
- Defect Rate: The percentage of defective units produced. A lower defect rate signifies improved quality.
- Inventory Levels: The amount of work-in-progress (WIP) and finished goods inventory. Reducing inventory minimizes storage costs and waste.
- Cost per Unit: The total cost associated with producing a single unit. Lowering the cost per unit improves profitability.
These KPIs should be tracked consistently over time to observe trends and measure the impact of implemented improvements.
Prioritizing Improvement Initiatives
With numerous potential areas for improvement, prioritizing initiatives strategically is crucial. A common approach is to use a prioritization matrix that considers both the potential impact and the effort required for each initiative. High-impact, low-effort projects should be tackled first, followed by those with high impact and high effort, and finally those with lower impact regardless of effort.
This ensures that resources are allocated efficiently to maximize the return on investment. Tools like a Value Stream Map can help visually identify the areas with the highest potential for improvement.
Examples of Successful Value Stream Improvement Projects, What is a value stream manager
A manufacturing company implemented Lean principles to reduce lead time in its assembly process. By eliminating unnecessary steps, improving material flow, and implementing a pull system (Kanban), they reduced lead time by 40% and increased throughput by 30%. Another example involves a software development team using Agile methodologies (a subset of Lean principles) and Scrum to improve their software delivery process.
By breaking down large projects into smaller, manageable sprints, they improved collaboration, reduced defects, and shortened delivery cycles significantly. A hospital used Six Sigma to reduce patient wait times in the emergency room. By analyzing the process and identifying bottlenecks, they implemented changes that reduced average wait times by 25%.
Collaboration and Communication
The Value Stream Manager’s role isn’t solely about process optimization; it’s deeply intertwined with fostering effective collaboration and communication across various departments and teams. Successfully implementing value stream improvements hinges on the ability to build consensus, manage expectations, and navigate inevitable conflicts. This requires a proactive and strategic approach to communication, emphasizing transparency and shared understanding.Effective communication within a value stream improvement initiative is crucial for its success.
Without clear and consistent communication, teams will struggle to align on goals, understand their roles, and contribute effectively. This section will explore strategies for achieving this.
Effective Communication Strategies for Cross-Functional Teams
Value stream managers need to employ diverse communication methods tailored to the audience and the message. Regular, concise updates, both formal and informal, are essential. Formal updates might include presentations to executive stakeholders outlining progress and challenges. Informal updates could involve quick check-ins with team members, using tools like daily stand-ups or instant messaging platforms. Visual aids, such as Kanban boards or progress charts, are invaluable in conveying complex information clearly and concisely.
Open forums, where team members can freely voice concerns and suggestions, promote a sense of ownership and collaboration. Finally, regular feedback mechanisms, both solicited and unsolicited, allow the value stream manager to adapt strategies and address issues promptly.
Building Consensus and Overcoming Resistance to Change
Change management is an integral part of value stream improvement. Resistance to change is common, stemming from fear of the unknown, disruption to established routines, or perceived threats to job security. To overcome this, the value stream manager must build a strong case for change, demonstrating the benefits clearly and transparently. This involves actively engaging stakeholders in the process, soliciting feedback, and addressing concerns directly.
Involving team members in the design and implementation of improvements fosters a sense of ownership and reduces resistance. Celebrating small wins along the way reinforces positive momentum and builds confidence in the overall initiative. Effective change management often involves a phased approach, allowing teams to adapt gradually to new processes and systems.
Stakeholder Management in Value Stream Improvement
Effective stakeholder management is paramount for the success of any value stream improvement project. This involves identifying all key stakeholders – from executives and department heads to front-line workers – and understanding their individual needs and concerns. A communication plan should be developed, outlining how and when each stakeholder group will be informed and engaged throughout the project lifecycle.
Regular meetings and progress reports are essential, ensuring transparency and accountability. Active listening and feedback mechanisms allow the value stream manager to address concerns promptly and adjust the project accordingly. Addressing the concerns of powerful stakeholders early on can prevent major roadblocks later in the process.
Effective Techniques for Conflict Resolution
Addressing conflicts promptly and constructively is vital for maintaining team morale and project momentum.
- Active Listening: Understanding all perspectives before attempting to resolve the issue.
- Facilitation: Guiding the discussion towards a mutually acceptable solution, focusing on shared goals.
- Mediation: If internal resolution fails, involving a neutral third party to help facilitate a resolution.
- Compromise: Finding solutions that address the needs of all parties involved, even if it means making concessions.
- Collaboration: Working together to find creative solutions that benefit the entire value stream.
Tools and Technologies Used by Value Stream Managers
Value stream managers rely on a robust toolkit of software and analytical methods to effectively map, analyze, and improve processes. The right tools empower them to visualize complex workflows, identify bottlenecks, and track progress toward leaner, more efficient operations. Choosing the right technology depends heavily on the organization’s size, industry, and specific needs.
Data analytics plays a crucial role in pinpointing areas ripe for improvement. By analyzing process data, value stream managers can uncover hidden inefficiencies and prioritize improvement initiatives based on their potential impact. This data-driven approach ensures that improvements are targeted and yield measurable results. Visualization techniques are equally important for effectively communicating findings and progress to stakeholders.
Software Tools for Value Stream Mapping and Analysis
Several software solutions facilitate value stream mapping and analysis. These tools often incorporate features for data collection, process modeling, simulation, and reporting. Popular options include specialized value stream mapping software, general-purpose process modeling tools, and even spreadsheet software like Microsoft Excel, depending on the complexity of the value stream. For example, some dedicated value stream mapping software allows for collaborative mapping, real-time data integration, and sophisticated analysis capabilities, providing a comprehensive view of the entire process.
More basic tools might require manual data entry and calculations, but can still be effective for smaller, simpler value streams.
The Role of Data Analytics in Identifying Areas for Improvement
Data analytics provides the quantitative insights necessary for effective value stream improvement. By collecting and analyzing data on process times, cycle times, defect rates, and inventory levels, value stream managers can identify bottlenecks, areas of waste, and opportunities for optimization. For example, analyzing cycle time data might reveal that a particular step in the process consistently takes significantly longer than others, indicating a need for process improvement in that specific area.
Similarly, analyzing defect rates can highlight quality control issues and identify areas where process improvements could reduce waste. This data-driven approach ensures that improvement efforts are focused on the most impactful areas.
Visualization Techniques for Communicating Value Stream Performance
Visual representations are critical for communicating complex information about value stream performance to a wide range of stakeholders. Value stream maps themselves are a primary visualization tool, clearly illustrating the flow of materials and information. In addition, charts, graphs, and dashboards can be used to present key performance indicators (KPIs) such as lead time, cycle time, and throughput.
These visuals provide a clear and concise overview of performance, enabling stakeholders to quickly grasp the current state and the impact of improvement initiatives. For instance, a simple bar chart could show the cycle time for each step in the process, immediately highlighting any bottlenecks.
Example of a Value Stream Map with Potential Improvement Areas
Imagine a simplified value stream map for processing customer orders. The map would begin with “Order Received” and proceed through steps such as “Order Processing,” “Inventory Check,” “Production,” “Quality Control,” “Packaging,” “Shipping,” and finally, “Order Delivered.” Each step would be represented by a box, with the time taken for each step indicated within the box. Arrows would connect the boxes, representing the flow of the order.
Let’s say the “Inventory Check” step takes an unusually long time compared to other steps. This would be highlighted in the map with a red circle or other visual indicator, signaling a potential bottleneck and area for improvement. Similarly, if the “Quality Control” step reveals a high defect rate, this too could be visually highlighted, prompting investigation and corrective action.
The map would also include key metrics such as lead time and cycle time, providing a holistic view of the process and its performance. This visual representation would allow for quick identification of areas needing attention and facilitate effective communication of the findings to stakeholders.
The Future of Value Stream Management
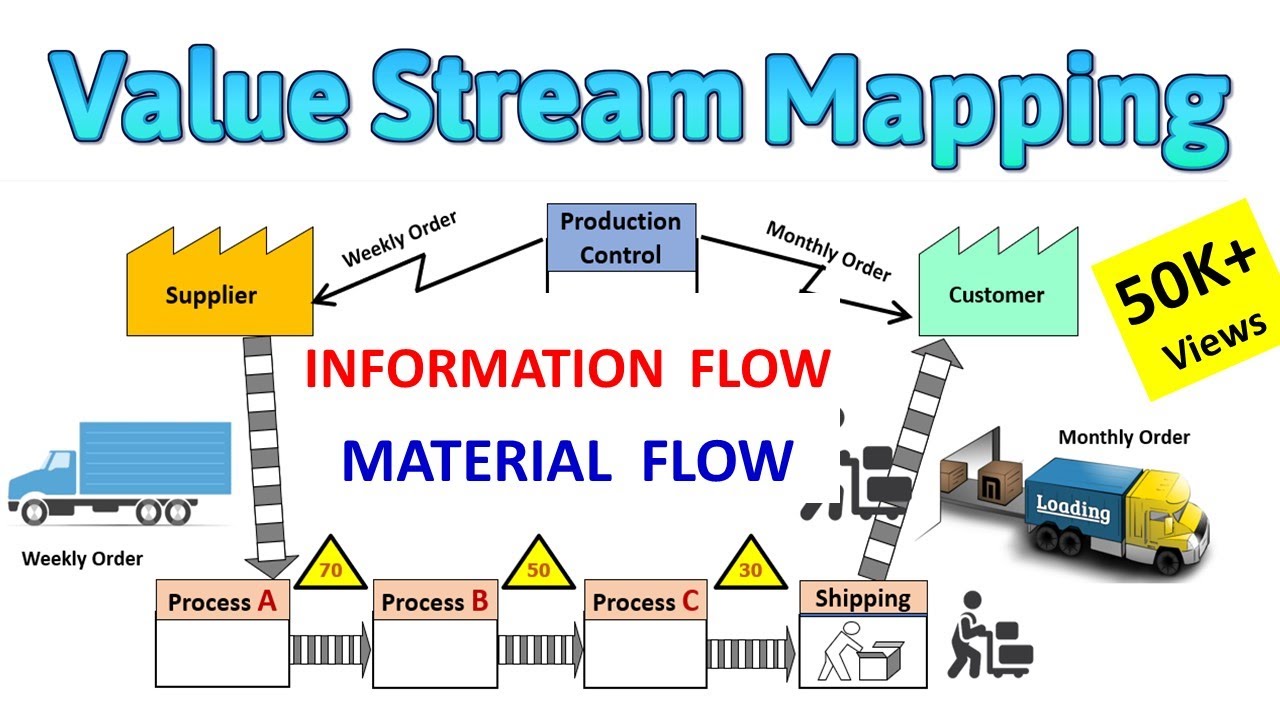
Value stream management (VSM) is rapidly evolving, driven by technological advancements and the increasing need for agility and efficiency in today’s dynamic business environment. The role of the value stream manager is also transforming, requiring a blend of traditional skills and new competencies to navigate the complexities of modern software development and operations. This section explores the emerging trends, challenges, and exciting possibilities shaping the future of VSM.
Emerging Trends and Challenges in Value Stream Management
Several key trends are reshaping the VSM landscape. The rise of AI and machine learning is automating many aspects of value stream mapping and analysis, leading to more accurate insights and faster identification of bottlenecks. However, this also presents challenges, such as the need for skilled professionals who can interpret and act upon AI-generated data, and ensuring the ethical and responsible use of AI in VSM.
Another significant trend is the increasing adoption of cloud-based platforms and tools, which offer greater scalability and flexibility but also introduce concerns about data security and integration with existing systems. Finally, the growing emphasis on sustainability is impacting VSM, requiring organizations to consider the environmental impact of their processes and optimize for both efficiency and reduced waste. For example, a manufacturing company might use VSM to identify and eliminate unnecessary transportation steps, thereby reducing its carbon footprint.
Evolution of the Value Stream Manager Role
The value stream manager role is evolving from a primarily operational role to one that requires strategic thinking and leadership. In the coming years, we can expect value stream managers to become more involved in cross-functional collaboration, leading initiatives to transform organizational culture and processes. They will need stronger analytical skills to interpret data from diverse sources, and more sophisticated communication skills to effectively convey complex information to both technical and non-technical audiences.
Furthermore, a deeper understanding of emerging technologies, such as AI and automation, will be crucial for effective VSM implementation. Imagine a value stream manager in a fintech company leading a project to improve customer onboarding, leveraging AI to analyze customer data and automate parts of the process while simultaneously ensuring regulatory compliance.
Technological Advancements Impacting Value Stream Management
Technological advancements are fundamentally changing VSM practices. AI-powered tools are automating value stream mapping, providing real-time visibility into process performance, and predicting potential bottlenecks. Advanced analytics are enabling organizations to identify and address inefficiencies with greater precision. Cloud-based platforms are facilitating collaboration and data sharing across teams and departments. The integration of IoT devices is providing granular data on physical processes, enabling more accurate and timely adjustments.
For instance, a logistics company could use IoT sensors on delivery trucks to monitor fuel consumption and route optimization in real-time, improving efficiency and reducing costs, all visible through the VSM dashboard.
Innovative Approaches to Value Stream Management in Different Industries
Innovative approaches to VSM are emerging across various industries. In software development, DevOps practices, combined with VSM, are accelerating delivery cycles and improving software quality. In manufacturing, lean manufacturing principles, integrated with VSM, are driving waste reduction and increased efficiency. In healthcare, VSM is being used to optimize patient flow, reduce wait times, and improve overall patient care.
A hospital, for example, could use VSM to analyze the patient journey from admission to discharge, identifying bottlenecks in the process and implementing improvements to reduce wait times and improve patient satisfaction. In the financial services industry, VSM is being used to streamline processes, reduce compliance risks, and enhance customer experience.
Final Wrap-Up: What Is A Value Stream Manager
So, what have we learned? A value stream manager is a crucial role in today’s business landscape, driving efficiency, reducing waste, and ultimately increasing profitability. Their ability to analyze processes, collaborate effectively, and implement improvements makes them invaluable assets. As businesses continue to prioritize optimization and customer satisfaction, the demand for skilled value stream managers will only continue to grow.
If you’re looking for a career that’s both challenging and rewarding, consider exploring this dynamic field.
Quick FAQs
What’s the difference between a Value Stream Manager and a Project Manager?
While both roles involve planning and execution, a project manager focuses on delivering a specific project within defined constraints. A value stream manager focuses on the long-term optimization of the entire process, encompassing multiple projects.
How much experience is typically required to become a Value Stream Manager?
It varies by industry and company, but generally, several years of experience in process improvement, operations, or a related field are needed. A strong understanding of Lean principles is often a prerequisite.
What software tools do Value Stream Managers commonly use?
Common tools include value stream mapping software (various options exist), data analytics platforms (like Tableau or Power BI), and project management software (like Jira or Asana).
Are certifications helpful for Value Stream Managers?
Yes, certifications like Lean Six Sigma Green Belt or Black Belt can significantly enhance a candidate’s credentials and demonstrate expertise in process improvement methodologies.