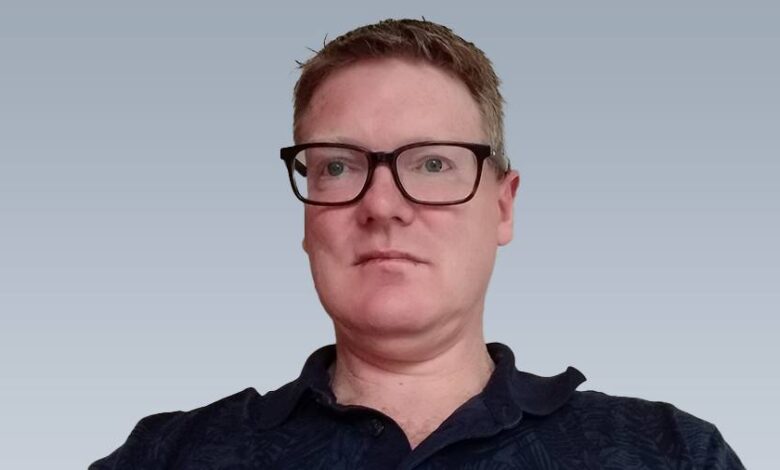
Cyber Attack on Australian Securities and Investments Commission
Cyber attack on Australian Securities and Investments Commission: The recent threat landscape highlights the vulnerability of even the most robust institutions. This isn’t just about numbers; it’s about the potential erosion of public trust and the significant disruption to Australia’s financial markets. We delve into the specifics of the potential threats, the devastating consequences, and the crucial steps needed to bolster ASIC’s cybersecurity defenses.
This isn’t a hypothetical exercise; it’s a vital discussion about safeguarding our financial future.
The Australian Securities and Investments Commission (ASIC) plays a critical role in regulating Australia’s financial markets. A successful cyberattack could compromise sensitive data, disrupt market operations, and severely damage public confidence. Understanding the potential vulnerabilities and implementing robust preventative measures is paramount. We’ll explore various attack vectors, from phishing scams to sophisticated malware, examining their potential impact and the necessary response strategies.
We’ll also look at the post-attack recovery process and the importance of collaboration between ASIC, law enforcement, and other stakeholders.
The Australian Securities and Investments Commission (ASIC) and Cybersecurity
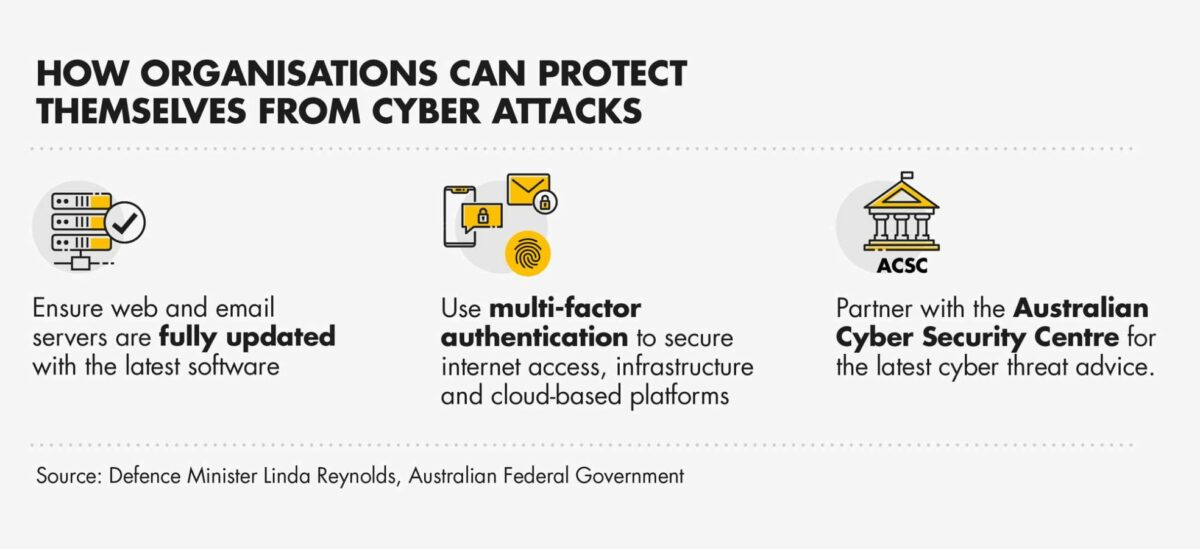
The Australian Securities and Investments Commission (ASIC) plays a crucial role in maintaining the integrity of Australia’s financial markets. Given its responsibility for overseeing a vast amount of sensitive financial data, ASIC’s cybersecurity posture is paramount to its operational effectiveness and the public trust. A breach could have far-reaching and devastating consequences for individuals, businesses, and the national economy.
Understanding ASIC’s cybersecurity infrastructure, vulnerabilities, and preventative measures is therefore essential.
ASIC’s Cybersecurity Infrastructure
ASIC, like other major financial institutions, likely employs a multi-layered cybersecurity infrastructure. This would include robust firewalls, intrusion detection and prevention systems (IDPS), data loss prevention (DLP) tools, and comprehensive endpoint security solutions for all its devices. They probably utilize advanced threat intelligence feeds to proactively identify and mitigate emerging threats. Furthermore, robust access control mechanisms, including multi-factor authentication (MFA), are likely in place to restrict access to sensitive data and systems.
Regular security audits and penetration testing are crucial components of their overall security strategy, ensuring ongoing vulnerability identification and remediation. Data encryption, both in transit and at rest, is another key element to protect sensitive information from unauthorized access. Finally, a comprehensive incident response plan would be essential to manage and contain any security breaches effectively.
Cyber Threats Facing ASIC
ASIC faces a range of sophisticated cyber threats. Phishing attacks, targeting employees with deceptive emails aiming to steal credentials or install malware, represent a significant risk. Ransomware attacks, encrypting critical data and demanding payment for its release, pose a serious operational disruption. Advanced persistent threats (APTs), often state-sponsored, can infiltrate systems undetected for extended periods, exfiltrating sensitive data or disrupting operations.
Distributed denial-of-service (DDoS) attacks, flooding ASIC’s systems with traffic to render them unavailable, can also severely impact its services. Finally, insider threats, either malicious or unintentional, remain a constant concern, highlighting the importance of strong access controls and security awareness training.
Potential Consequences of a Successful Cyber Attack on ASIC
A successful cyber attack on ASIC could have severe consequences. Data breaches could expose sensitive personal and financial information of individuals and businesses, leading to identity theft, financial losses, and reputational damage for ASIC and the affected parties. Disruption of ASIC’s operations could undermine market confidence, potentially triggering instability in the financial markets. The loss of critical data could hamper ASIC’s regulatory functions, impacting its ability to monitor and enforce compliance, ultimately threatening the integrity of the Australian financial system.
Furthermore, legal and regulatory repercussions, including significant fines and reputational damage, could follow a significant breach. The overall economic impact on Australia could be substantial. For example, a significant breach impacting investor confidence could lead to a downturn in the stock market and broader economic instability.
Preventative Measures for ASIC
To strengthen its defenses, ASIC could implement several preventative measures. Enhanced employee security awareness training, focusing on phishing and social engineering tactics, is crucial. Regular security audits and penetration testing, using both internal and external experts, can identify and address vulnerabilities before they are exploited. Implementing a zero-trust security model, verifying every user and device before granting access, regardless of network location, would significantly enhance security.
Investing in advanced threat detection and response capabilities, including artificial intelligence (AI) and machine learning (ML) based solutions, can help proactively identify and neutralize threats. Strengthening collaboration with other regulatory bodies and intelligence agencies to share threat information and best practices is also vital. Finally, a robust incident response plan, regularly tested and updated, is crucial for effective mitigation and recovery in the event of a successful attack.
Types of Cyber Attacks Targeting ASIC
ASIC, as a key regulator in Australia’s financial markets, is a prime target for cyberattacks. The sensitive data it holds – including personal financial information, company records, and market intelligence – makes it a lucrative target for various malicious actors, from financially motivated cybercriminals to state-sponsored actors. Understanding the likely attack vectors and their potential impact is crucial for effective cybersecurity strategies.
Likely Attack Methods Against ASIC, Cyber attack on australian securities and investments commission
Several attack methods pose significant threats to ASIC’s systems. These range from relatively simple, widely used techniques to highly sophisticated, targeted attacks requiring substantial resources and expertise. The consequences of a successful attack can be severe, ranging from data breaches and financial losses to reputational damage and disruption of essential regulatory functions.
Phishing Attacks
Phishing attacks remain a persistent and effective threat. These attacks typically involve deceptive emails or websites designed to trick ASIC employees into revealing sensitive credentials, such as usernames, passwords, or multi-factor authentication codes. A successful phishing campaign could grant attackers access to internal systems, allowing them to steal data, install malware, or disrupt operations. The impact on ASIC’s operations could include data breaches, compromised internal communications, and operational downtime.
The sophistication required for a successful phishing attack can vary, from relatively simple mass-email campaigns to highly targeted spear-phishing attacks using sophisticated social engineering techniques.
Malware Infections
Malware, encompassing viruses, ransomware, and spyware, poses a significant threat. Malware can be introduced through various means, including malicious email attachments, infected websites, or compromised software. Once installed, malware can steal data, encrypt files (ransomware), or monitor user activity (spyware). The impact of a malware infection could be devastating, leading to data loss, operational disruption, significant financial losses (particularly in the case of ransomware), and reputational damage.
The sophistication of malware attacks can range from simple, easily detectable malware to advanced, polymorphic malware designed to evade detection and exploit system vulnerabilities. The resources required also vary greatly, from readily available malware kits to custom-developed malware requiring significant expertise.
Denial-of-Service (DoS) Attacks
DoS attacks aim to overwhelm ASIC’s systems with traffic, rendering them unavailable to legitimate users. These attacks can be relatively simple to launch using readily available tools, or highly sophisticated, involving distributed denial-of-service (DDoS) attacks coordinated across a vast network of compromised computers (botnet). The impact of a successful DoS attack could range from minor service disruptions to a complete shutdown of ASIC’s online services, impacting market operations, investor confidence, and ASIC’s ability to perform its regulatory functions.
The resources required for DoS attacks vary considerably, from readily available tools for simple attacks to significant resources and expertise for large-scale DDoS attacks.
Hypothetical Cyber Attack Scenario: Breach of ASIC’s Database
The following table details a hypothetical scenario illustrating a successful cyberattack on ASIC’s database:
Stage | Impact | Response | Timeline |
---|---|---|---|
Initial Compromise (Spear-phishing targeting a senior employee) | Compromised employee credentials grant initial access to the internal network. | Implement robust multi-factor authentication, enhanced security awareness training. | 1-2 days |
Lateral Movement (Attacker moves within the network) | Access to sensitive internal systems and data, including the database. | Intrusion Detection/Prevention System (IDS/IPS), network segmentation, regular security audits. | 3-7 days |
Data Exfiltration (Attacker copies sensitive data) | Loss of confidential data (personal financial information, market intelligence, etc.). | Data Loss Prevention (DLP) tools, regular data backups, encryption of sensitive data. | 1-2 weeks |
Ransomware Deployment (Attacker encrypts data) | Database becomes inaccessible, operations are disrupted. | Regular backups, offline backups, incident response plan, negotiation with attackers (if deemed appropriate). | Immediate |
Data Breaches and Their Impact: Cyber Attack On Australian Securities And Investments Commission
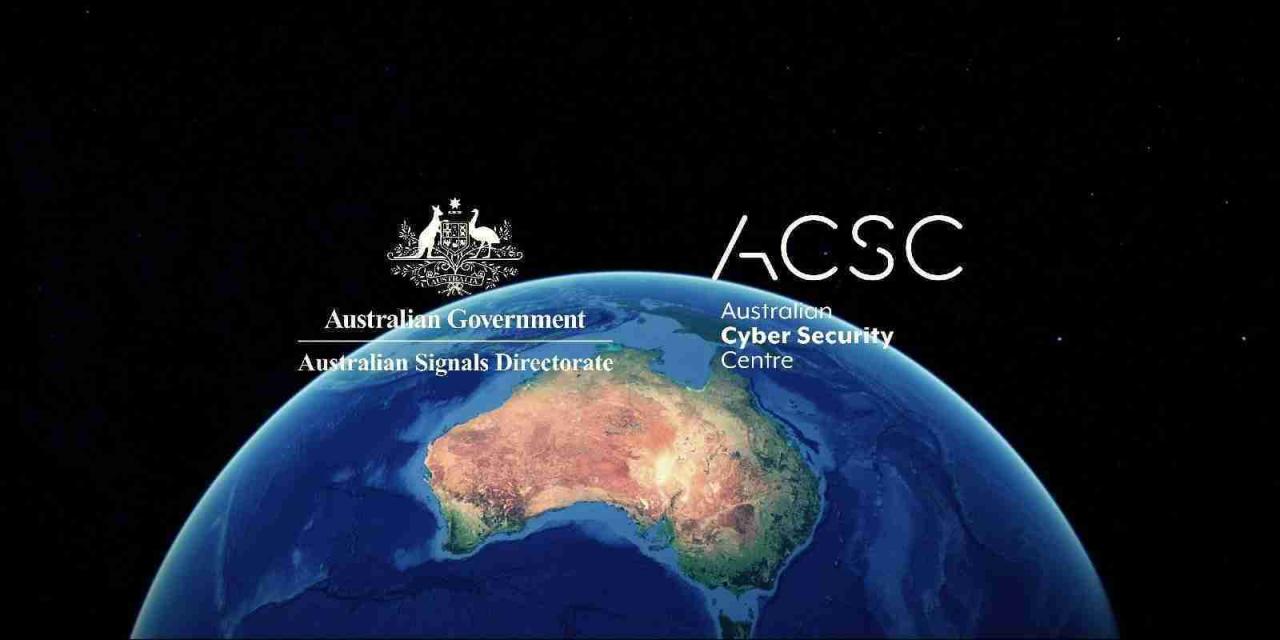
A cyberattack on the Australian Securities and Investments Commission (ASIC) could have devastating consequences, primarily through data breaches. The sheer volume and sensitivity of the data ASIC holds make it a prime target for malicious actors, and a successful breach would have far-reaching implications for individuals, businesses, and the Australian economy as a whole. Understanding the potential types of data at risk, the resulting legal and financial ramifications, and appropriate responses is crucial for mitigating the damage.
The recent cyber attack on the Australian Securities and Investments Commission highlights the urgent need for robust, secure systems. Building those systems faster and more efficiently is crucial, which is why I’ve been researching platforms like Domino, as detailed in this insightful article on domino app dev the low code and pro code future. The potential for rapid development offered by low-code/pro-code solutions could be a game-changer in protecting against future attacks on organizations like ASIC.
Types of Sensitive Data Held by ASIC
ASIC manages a vast amount of sensitive information crucial to the integrity of Australia’s financial markets. This includes confidential financial records of companies listed on the Australian Securities Exchange (ASX), detailed personal information of investors (such as addresses, tax file numbers, and banking details), and regulatory filings containing commercially sensitive business strategies and financial projections. Breaches could expose intellectual property, trade secrets, and sensitive details about ongoing investigations.
The potential for identity theft, financial fraud, and market manipulation is significant. A breach impacting superannuation details would also have profound implications for millions of Australians.
Legal and Reputational Consequences for ASIC Following a Data Breach
A data breach at ASIC would trigger significant legal repercussions. ASIC is subject to the Privacy Act 1988 and the Notifiable Data Breaches scheme, mandating notification to affected individuals and the Office of the Australian Information Commissioner (OAIC). Failure to comply could result in substantial fines. Beyond legal penalties, the reputational damage would be immense. Loss of public trust in ASIC’s ability to safeguard sensitive data would undermine its credibility and effectiveness as a regulator.
This could lead to decreased investor confidence, impacting market stability and potentially triggering a negative economic cycle. The cost of restoring public trust would be substantial and long-term.
The recent cyber attack on the Australian Securities and Investments Commission (ASIC) highlights the urgent need for robust cybersecurity measures. Understanding how to effectively manage cloud security is crucial, and that’s where solutions like those discussed in this article on bitglass and the rise of cloud security posture management become invaluable. Strengthening cloud security posture is no longer optional; the ASIC breach serves as a stark reminder of the potential consequences of failing to do so.
Financial Ramifications of a Data Breach for ASIC and the Australian Economy
The financial impact of an ASIC data breach would be multifaceted. ASIC would incur direct costs related to incident response, legal fees, notification costs, credit monitoring services for affected individuals, and potential compensation claims. Indirect costs, including reputational damage and loss of productivity, could be far greater. For the broader Australian economy, the consequences could be severe.
A loss of investor confidence could lead to market volatility, reduced investment, and economic downturn. The cost of mitigating the damage to the financial system, including potential fraud investigations and financial recovery efforts, would be substantial and borne by taxpayers. The 2017 Equifax breach, which exposed the personal data of nearly 150 million people, cost the company billions of dollars and severely damaged its reputation – serving as a stark example of the potential financial fallout.
Potential Responses ASIC Should Implement Following a Confirmed Data Breach
Following a confirmed data breach, ASIC needs a comprehensive and swift response. This includes:
- Immediately securing the affected systems and containing the breach to prevent further data exfiltration.
- Conducting a thorough forensic investigation to determine the extent of the breach and identify the source.
- Notifying affected individuals and the OAIC in accordance with the Notifiable Data Breaches scheme.
- Offering credit monitoring and identity theft protection services to affected individuals.
- Cooperating fully with law enforcement agencies in any criminal investigation.
- Implementing robust remediation measures to prevent future breaches, including enhanced cybersecurity infrastructure and employee training.
- Conducting a thorough post-incident review to identify weaknesses and improve security protocols.
- Publicly communicating the incident and the steps taken to address it, maintaining transparency and building trust.
Response and Recovery Strategies
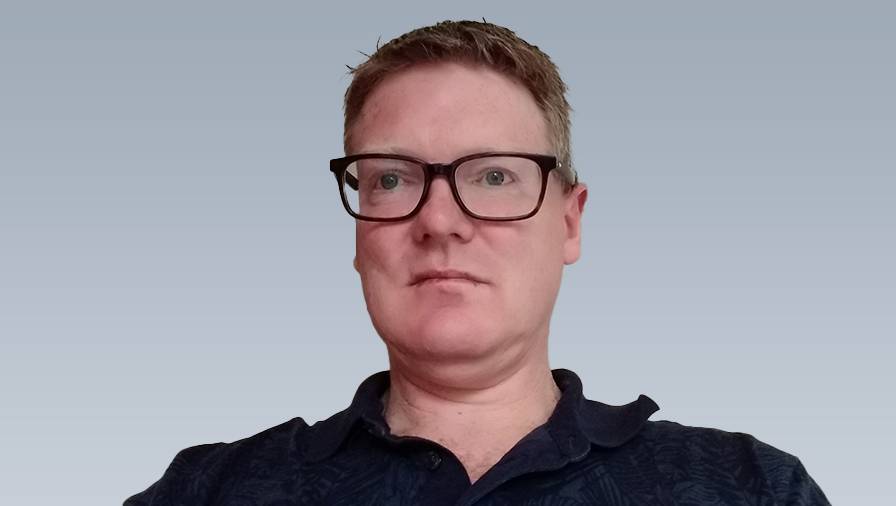
A swift and effective response is crucial in mitigating the damage from a cyberattack on an organization as vital as ASIC. Failure to act decisively can lead to significant financial losses, reputational damage, and erosion of public trust. A robust incident response plan, coupled with proactive security measures, is paramount for minimizing the impact of such an event.
ASIC’s response and recovery strategy must be multifaceted, encompassing real-time detection, rapid containment, and thorough investigation to identify the root cause and vulnerabilities exploited. This strategy needs to be well-rehearsed through regular simulations and updates to reflect evolving threat landscapes.
Real-time Detection and Response to Cyber Attacks
Real-time detection relies on a sophisticated network of security tools and skilled analysts. This includes intrusion detection systems (IDS), security information and event management (SIEM) systems, and endpoint detection and response (EDR) solutions. These tools constantly monitor network traffic and system activity for suspicious patterns. ASIC should employ a Security Operations Center (SOC) staffed by highly trained cybersecurity professionals capable of analyzing alerts, investigating incidents, and responding effectively in real-time.
Automated responses, such as isolating infected systems or blocking malicious traffic, should be implemented where possible to minimize the impact of the attack. Furthermore, regular penetration testing and vulnerability assessments are crucial for identifying weaknesses before attackers can exploit them. The response must also include a clear escalation path, ensuring that senior management is promptly informed of significant incidents.
ASIC’s Incident Response Plan
An effective incident response plan Artikels roles, responsibilities, and communication protocols for handling cyberattacks. This plan should clearly define the roles of different teams, including the SOC, legal counsel, public relations, and senior management. Each team member should have clearly defined responsibilities and escalation procedures. A communication protocol should be established to ensure clear and timely communication both internally and externally, including updates to stakeholders, affected parties, and the media.
The plan must also Artikel procedures for evidence preservation, forensic investigation, and system restoration. Regular tabletop exercises and simulations should be conducted to test the plan’s effectiveness and identify areas for improvement. Consider a scenario like the 2017 NotPetya ransomware attack, where swift response and coordination between affected organizations were crucial in limiting the overall damage.
Collaboration with Law Enforcement and Other Agencies
Collaboration is vital in the event of a major cyberattack. ASIC should have established relationships with law enforcement agencies (such as the Australian Federal Police), cybersecurity agencies (such as the Australian Cyber Security Centre), and other relevant organizations. This collaboration allows for the sharing of intelligence, coordination of investigations, and the pooling of resources to effectively respond to and mitigate the threat.
Open communication channels are crucial for efficient information exchange and coordinated action. In the event of a significant attack, involving critical infrastructure or sensitive data, a joint task force might be necessary. For example, the response to the 2012 Sony Pictures cyberattack highlighted the importance of collaboration between the affected company, law enforcement, and intelligence agencies.
ASIC’s Incident Response Process Flowchart
The following describes a flowchart illustrating the stages of ASIC’s incident response process. Each stage is detailed below:
Stage 1: Detection and Identification
-This stage involves the detection of a potential security incident through various security tools and monitoring systems. The initial alert is analyzed to determine if it represents a genuine threat.
Stage 2: Analysis and Containment
– Once a threat is confirmed, the nature and scope of the attack are determined. Immediate steps are taken to contain the threat, such as isolating infected systems or blocking malicious traffic. This stage also involves data gathering and evidence preservation.
Stage 3: Eradication and Recovery
-This stage focuses on removing the malware, restoring affected systems, and patching vulnerabilities. Data recovery and system restoration plans are activated.
Stage 4: Post-Incident Activity
-This involves a thorough review of the incident to identify root causes, vulnerabilities, and lessons learned. The incident response plan is updated based on the findings. Communication with stakeholders continues, and remediation efforts are finalized.
Stage 5: Reporting and Communication
– Regular updates are provided to relevant stakeholders, including senior management, law enforcement, and affected parties. A final report is prepared documenting the incident, its impact, and the actions taken.
Preventing Future Attacks
The Australian Securities and Investments Commission (ASIC) plays a vital role in maintaining the integrity of Australia’s financial markets. A successful cyberattack against ASIC could have devastating consequences, impacting investor confidence and potentially causing significant financial losses. Therefore, proactively strengthening ASIC’s cybersecurity posture is not just important, it’s paramount. This requires a multi-faceted approach encompassing technological upgrades, robust security protocols, and a highly trained and vigilant workforce.
A layered security approach is crucial to mitigate the risk of future attacks. This involves a combination of preventative measures, detection systems, and incident response plans. By focusing on strengthening these three key areas, ASIC can significantly reduce its vulnerability to cyber threats and improve its overall resilience.
Recommendations for Enhancing ASIC’s Cybersecurity Posture
ASIC needs a comprehensive strategy that goes beyond simple updates and patches. It requires a proactive and adaptable approach to security, constantly evolving to stay ahead of emerging threats. The following recommendations highlight key areas for improvement.
- Implement a Zero Trust Security Model: This model assumes no implicit trust granted to any user, device, or network, regardless of location. Verification is required at every access point, significantly reducing the impact of compromised credentials.
- Enhance Threat Intelligence Capabilities: Proactive threat hunting and analysis are vital. ASIC should invest in advanced threat intelligence platforms to identify and mitigate emerging threats before they can impact the organization.
- Strengthen Network Security: This includes implementing robust firewalls, intrusion detection and prevention systems (IDS/IPS), and regularly updating network security protocols. Regular penetration testing should also be conducted to identify vulnerabilities.
- Improve Data Loss Prevention (DLP): ASIC needs to implement strong DLP measures to prevent sensitive data from leaving the organization’s controlled environment without authorization. This includes encryption, access controls, and monitoring of data transfers.
- Regular Security Audits and Penetration Testing: Independent security audits and penetration testing should be conducted regularly to identify vulnerabilities and ensure that security controls are effective. These should be conducted by external experts to provide an unbiased assessment.
The Role of Employee Training and Awareness in Preventing Cyber Attacks
Even the most robust technological security measures can be bypassed by a well-crafted social engineering attack. Therefore, investing in comprehensive employee training and awareness programs is crucial. This should not be a one-time event but an ongoing process of education and reinforcement.
Training should cover various aspects of cybersecurity, including phishing awareness, password security, social engineering tactics, and safe browsing practices. Regular simulated phishing exercises can help employees identify and report suspicious emails. Furthermore, clear reporting procedures for security incidents should be established and regularly communicated.
Benefits of Implementing Multi-Factor Authentication and Other Security Measures
Multi-factor authentication (MFA) adds an extra layer of security by requiring users to provide multiple forms of authentication before gaining access to systems or data. This significantly reduces the risk of unauthorized access, even if passwords are compromised. Other security measures such as encryption, access controls, and regular software updates also play a vital role in strengthening overall security.
Implementing MFA can significantly reduce the risk of successful phishing attacks and other credential-based attacks. For example, even if an attacker obtains a user’s password through phishing, they would still be unable to access the system without the second factor of authentication, such as a one-time code sent to a mobile device.
Hypothetical Image Depicting a Successful Security Awareness Training Program
Imagine a brightly lit, modern training room at ASIC headquarters. Employees from various departments are actively participating in a cybersecurity awareness workshop. The atmosphere is relaxed yet focused, with interactive elements such as quizzes and group discussions. A facilitator, a cybersecurity expert, is engaging the audience using real-life examples of cyberattacks and demonstrating how to identify and avoid common threats.
Large screens display engaging visuals, including animated scenarios showing the consequences of poor security practices. The overall mood is positive and empowering, with employees feeling confident and equipped to handle cybersecurity challenges. Participants are actively taking notes and asking questions, demonstrating their engagement and understanding of the training material. The room is filled with a sense of collective responsibility and proactive security awareness.
Outcome Summary
The threat of a cyber attack on ASIC is a serious concern, demanding a proactive and multi-faceted approach to cybersecurity. From strengthening infrastructure and employee training to implementing robust incident response plans, safeguarding ASIC is crucial for maintaining the integrity of Australia’s financial system. This isn’t just about protecting data; it’s about protecting the public’s trust and the stability of our economy.
The future of our financial markets depends on our collective ability to anticipate and effectively mitigate these threats.
Clarifying Questions
What types of data are most at risk in an ASIC cyberattack?
Sensitive data like investor personal information, financial records, and market-sensitive data are all prime targets.
What is ASIC’s current cybersecurity infrastructure like?
While the specifics are confidential for security reasons, ASIC likely utilizes a multi-layered approach encompassing firewalls, intrusion detection systems, and data encryption.
What role does employee training play in preventing cyberattacks?
Employee training is critical. Educating staff about phishing scams, malware, and safe password practices significantly reduces the risk of human error, a major vulnerability.
What happens if a data breach occurs?
A breach would trigger an immediate incident response plan, including data recovery, legal action, and notification of affected individuals and authorities.
How does a successful cyberattack impact the Australian economy?
A major breach could cause market instability, loss of investor confidence, and significant financial losses, impacting the broader Australian economy.